Introduction
Dry-docking of a vessel is required at every 5 yearly intervals to carry out inspection of hull, propeller and other components which are normally submersed in water all the time. This is a requirement by ship’s classification societies. However, some owners prefer to do it every 30 months to ensure good performance and minimum downtime of vessels when they are in service.
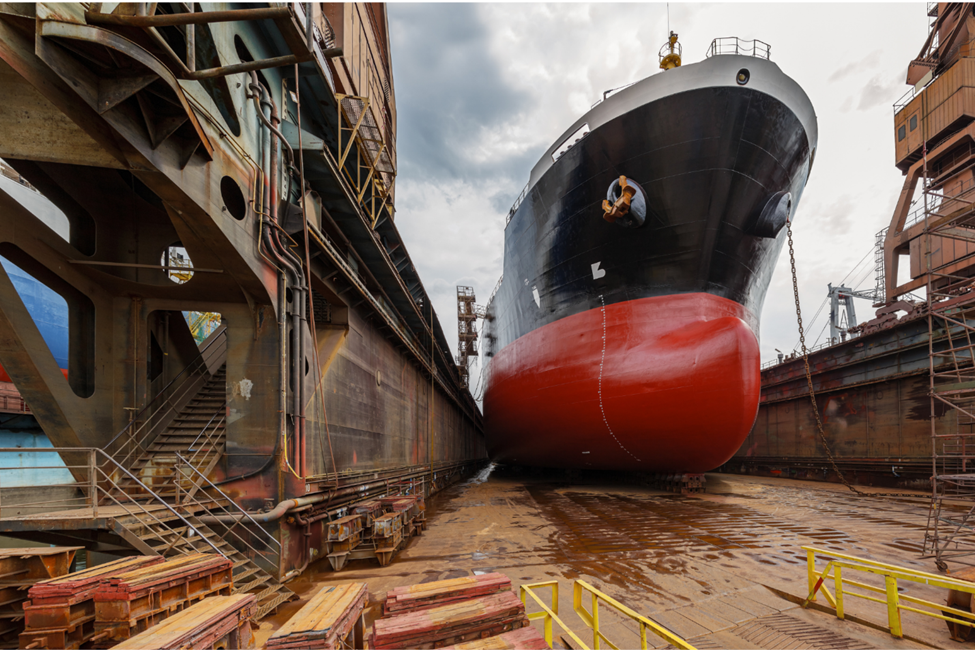
General Preparations for dry-docking
Good planning is very much necessary to address all pertaining issues during docking. Close coordination with in charge superintendent is necessary at all times. Following points should be borne in mind when finalizing the specification for docking:
- We need to go through the ship’s classification survey status report and identify the jobs which are required to be done. If any doubt; the in-charge superintendent to be consulted. For some of the identified jobs may be some spares / shore technician attendance will be required.
- Once the surveyor is appointed, the Superintendent should consult him and appraise him of the planning. The surveyor in return shall advise if there are any other additional requirements like some checks / inspections necessary as per any new rule. The docking planning should contain all these items.
- It is a saying that when a docking finishes; the preparation for next docking starts. The on-board system should be such that all deficiencies or breakdowns should be reported. In case something cannot be permanently repaired; those items should be addressed during docking. Hence; all these items should be included in the docking specification. The docking specification should be raised in easy language such that it is easy for understanding for the dock people. It is advised to include smallest of the details which can be useful for dock people. For example; if a pipeline is to be renewed – the dimension of pipe, the flanges, number of bolts and if there is any other sub-job like removing of floor plates, cutting of angle bars for free access etc also to be mentioned. The specification should be supplemented with representative pictures.
- The ship’s PMS program should be checked such that all major jobs are taken care of in the planning.
- It’s a good foresight that we should address those issues with priority which cannot be done when vessel is afloat or which require off-hire.
- Once the docking specification finalizes; the requisitions for spares and services to be raised.
- We should always keep in mind that extra jobs may pop up even after finalizing the docking specification. All these extra jobs to be conveyed to office for approval and in-charge superintendent will forward the same to the dockyard.
- There are many jobs which the ship staff can do during docking – a list to be prepared and to be kept ready. Minor tank cleanings; inspections etc. should be identified and a comprehensive list should be prepared. It’s better to assign minimum direct work to ship staff as they will be mostly busy with supervision of various jobs.
- Once the dockyard is fixed, we should go through the yard specific requirements and comply with them prior coming to yard. This may include marking of bunker tanks on main deck which are not gas free and containing oils. Isolation procedure for fixed fire fighting system to be checked as the yard will require this upon arrival.
Vessel Specific Preparations
For an oil tanker; it is required to make the tanks gas free upon arrival at yard. For crude oil tankers where the tank cleaning does not take place during normal running; good tank cleaning is must to have clean and gas free tanks. The process includes tank cleaning by fixed tank cleaning machines; purging and then gas freeing. All associated equipment for these processes should be working in good condition. Remember that use of both Inert Gas blowers will be required. The superintendent may plan for tank inspection by floating boats in tank. The riding team should be assisted accordingly as this process will require controlled filling and emptying of cargo tanks. The Chief Officer has to ensure good stability condition for complete operation. Once the tank inspection job is completed; the filled water to be discharged as per regulation through Oil Discharge Monitoring & Control System.
Best practices
The riding team (thickness gauging) should be utilized for various measurements in engine room like overboard pipe sections; engine room double bottom tanks and other areas which have direct bulkhead with sea. Any probable deficiency should be included in the additional job specification.
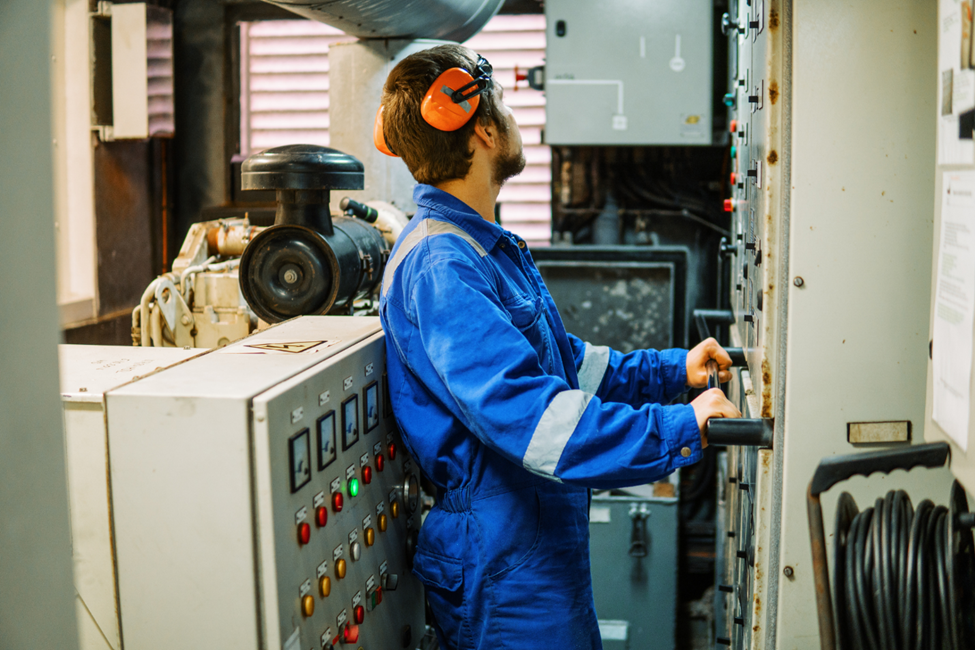
One important aspect for docking is the stowage of fuel oil as per the permissible stability when the vessel will rest on blocks during dry docking. Also; the ROB of Diesel Oil to be topped up as all system will be changed over to diesel oil prior entering docks. Training of all engineers on safe fuel changeover procedure is recommended.
It’s better to keep the boiler water tanks topped up as during docks it’s difficult to get distilled water but portable water supply is no issue.
In this way, by thinking about smaller details; we can address all issues and have a smooth docking time.
Author’s profile
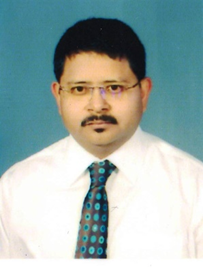
Vikas is having 24 years of experience as Marine Engineer. He is presently sailing as Chief Engineer on Oil / Gas Tankers with Mitsui OSK Lines. In past; he has worked as “Vessel Manager” with a renowned company at Singapore providing technical support to fleet vessels. His passion for seafaring brought him back to sea again.
At this juncture of his career, he likes mentoring young cadets onboard. He likes writing short columns on practical aspects of Marine Engineering.
Please register or login to read the full article
Thankyou sir for sharing your valuable inputs and experience about docking, sure it will help us in great way fro preparation for drydock.
Great job sir. Very useful informations collected and shared with us.
Very informative and useful,thanks for sharing.
A very useful article sir indeed. Will definitely help in preparing the vessel for dry docking in a better planned way.