By Alan Crowle, BSc, MSc, CEng, CMarEng, FRINA, FMAREST, FSCMS
Masters by Researcher, University of Exeter, College of Engineering, Mathematics and Physical Sciences, Renewable Energy Group
Summary
Floating offshore wind turbines are an emerging source of marine renewable energy. Installation preparation checklists of these large floating structures are required to provide confidence to owners and insurers that they are constructed in a safe and cost effective manner. The checklists developed in this article cover the substructure types such as barges, Spars, semi submersibles and tension leg platforms (TLPs). This article details the preparation requirements for installation vessels, large onshore cranes and for the floating substructures that support the offshore wind turbines.
Floating offshore wind can take advantage lessons learnt from offshore oil and gas industry and fixed offshore wind experience in enabling installation techniques to be developed during loadout, ocean tow and installation. The installation process for a floating wind turbine varies with substructure type and this article will give an overview and comparative analysis of installation methods.
The scope of work for the naval architect for the transport and installation of the floating substructures and subsea infrastructure is discussed. The naval architecture work includes feasibility studies, transport and installation reports, preparation of design basis and review of port information. The preparation for the offshore installation also involves vessel suitability and approval of equipment.
Naval architecture input
Floating offshore wind turbines require high capital expenditure before there is any return on investment. Therefore careful preparations are required during marine construction, ocean transport and offshore installation, to provide confidence to owners, local authorities and insurers.
Preparations are required in the following areas, to minimize the risks to people, installation vessels, the floating structure and the environment and can be listed as follows:
- Loadout of the topsides components namely blades, nacelles, towers
- Ocean transport of the topsides to the fit out yard
- Loadout, transportation and offshore installation of mooring components
- Loadout, transportation and seabed laying of export cables, their burial and seabed protection
- Loadout, or float out, of the substructure from a shipyard and transport to the fit out yard
- On shore storage of components on a fit out quay
- Wet storage of the substructure before mooring to the fit out quay
- Mooring of substructure at the fit out quay
- Lifting of topside components (tower, nacelle and blades)
- Probable wet storage in sheltered waters of the completed structure.
- Tow out of the completed structure
- Connection of moorings to the completed structure
- Loadout, ocean transport and laying the export cable and its burial on the seabed
- Loadout, transportation and offshore installation of the inter array dynamic cable
- Connection of the dynamic cables to the completed structure
Types of floating offshore wind turbines
The main types of floating offshore wind turbines are shown in figures 1.
It is intended that semi submersible and barge types are fully fitted out alongside a quay prior to tow out offshore. Spar types are fitted out in sheltered deep water before being towed offshore for final installation. Tension leg platforms (TLPs) are at an early stage of development and so naval architecture guidelines are still being considered. Some TLP installation options involve use of temporary buoyancy or large crane vessels with active heave compensation.
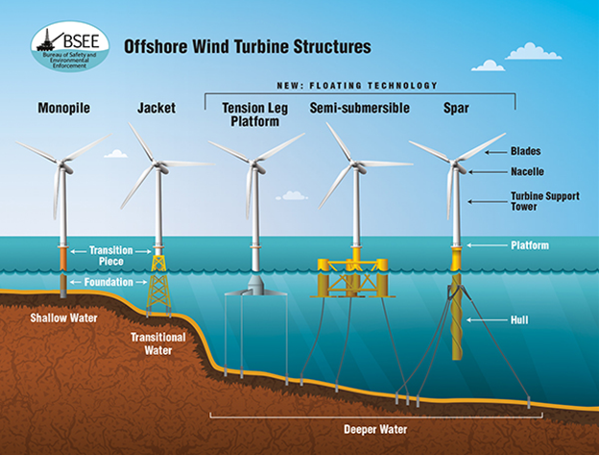
Generally, it is assumed that floating wind farms will be installed at depths that fixed foundations cannot reach for technical or economic response. However, the depth boundary between fixed and floating wind farms is becoming blurred. New configurations are being studied to allow floating platforms to be installed in relatively shallow waters, specifically in locations where seabed conditions pose a risk to the installation of fixed platforms. Currently, it is technically feasible to install floating platforms between 60 and 300 meters, and studies are underway to extend this range to shallower waters, up to 800 meters, although this is not economically viable at present. Fixed platforms, monopoles and jackets, are being designed up to water depths of 80metres based increased capability of wind turbine installation vessels.
Vessel survey
The naval architect conducts surveys of transport vessels, anchor handling tugs and crane vessels, to assess their suitability for cargo transportation, or capability of a tug for towing. During the survey, the naval architect will use all the pertinent project information, e.g., transportation route (inshore and offshore), bathymetrical data of the route, weather condition during tow. Vessel specific information, such as condition of the vessel, lightship characteristics, certificates of classification society and other regulatory agencies, pumping capabilities, bollard pull of tug, capacity of deck of transport vessels are checked. On-hire and Off-hire surveys are carried out to compare the condition of the vessels before and after the specific contract or phase to see if there was any damage to the vessel during the marine operation.
A review of certificates (depending on the specific marine operation) includes but not limited to, certificates of crane including crane capability radius and lifting chart, slings, shackles, pin, jacking system, mooring ropes (wire and/or chain), winches, valid classification certificates, bollard pull certification, weighing certificates, any test certificate, including planned maintenance routines.
Naval architecture services are frequently sought for the following three types of marine/offshore projects for the test and trial of floating vessels, inshore moorings, wet storage, ocean towage and offshore operations
This paper primarily covers offshore marine operations related to loadout, transportation, and installation of fixed jacket type structure.
RESTRICTIONS
The ocean transport, over long distances, of blades, nacelles and towers is based on unrestricted weather conditions using 1 in 10 year weather conditions. The naval engineering nomenclature used are as follows:
- Linear movements in the horizontal direction: Surge and sway.
- Movement in the vertical direction: Heave
- Angular movements: Roll, yaw and pitch.
The tow out of the completed structure is considered to be a restricted weather operation which needs to be completed within the limits of an operational reference period with a weather forecast not exceeding the operational criteria. The operational reference period (which includes contingencies) is generally less than 72 hours. The design environmental condition need not reflect the statistical extremes for the area and season. These motions have to be minimized to avoid accelerations at the turbine level, which is more than 120 meters above sea level. A small angular displacement at the level of the floating platform, for example, translates into a large linear movement at the highest point of the structure, which, if not controlled, can damage and reduce the lifetime of the mechanical elements located in the nacelle.
INSTALLATION
The mooring options may be drag anchor, suction pile, drilled pile, drilled pile or gravity. The mooring lines may be: all chain, chain on the seabed and close to the substructure and wire between the chain or chain on the seabed and close to the substructure and synthetic fiber. Mooring lines are pre laid prior to the arrival of the completed floating offshore wind turbine.
The choice of mooring type depends on water depth, weather conditions (wave, wind, tide) and substructure type. The mooring line may be chain, steel wire or synthetic rope, or a combination of these materials. Moorings may be catenary or taut and used on barges, spars and semi submersibles. TLP anchorages are tendons that function differently from tensioned catenaries. They are suitable for large depths due to the material savings involved.
Export cable installation naval architecture includes of load-out onto cable lay vessel, cable laying and burial. Dynamic cable installation can only take place when the floating offshore wind turbine and the export cable have been installed.
The substructure delivery includes load-out onto a heavy transport vessel, or alternatively float out from a drydock. Then there is the dry transport of the substructure from the shipyard and checks are required water depth, available air draft, possible piracy and canal locks. Float off from the heavy transport vessel takes place near the fit out quay, followed by mooring the substructure at the fit out quay
Lifting of the topside components, at the fit out quay, can be using a land based crane which requires checking the strength of the quay or by using a floating crane vessel to lift the topside components. This lifting of heavy components is restricted to wind speeds of less than about 10m/s. The tow out of the completed structure requires a large bollard pull anchor handling tug with the assistance of harbor tugs, Figure 2 shows a semi submersible at the start of tow out from the fit out quay, at a draft of about 10 to 12m. Figure 3 shows a completed steel Spar under tow with a draft of 70 to 90m. The connection of the pre laid moorings offshore requires three large anchor handling tugs.
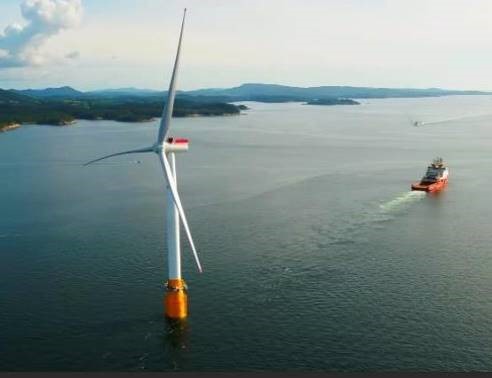

OPERATION
Naval architecture calculations are required for intact stability, damage stability, in place motions and fatigue life. Mooring calculations are required for all weather conditions, including the loss of one mooring line.
Possible heavy maintenance, for TLPs and Spars is expected to be carried out offshore on the floating offshore wind turbine. However, for semi submersibles and barge types, disconnection of moorings and dynamic array cables electrical cables can be considered, and then the vessel can return to port for heavy maintenance.
CONCLUSION
Floating offshore wind is a simple concept with a big future. It means that wind turbines can be installed into deeper waters, than fixed wind turbines, where the winds are stronger and more reliable. Further offshore, the wind turbines have less environmental and visual impact, at the offshore location. It has a very big role to play if countries are to achieve their net zero targets.
Many countries do not have shallow coastal waters. As a consequence, floating wind will be the only solution if these nations wish to deliver offshore renewables. The USA west coast and Japan are a good examples of this. Other countries that will benefit from floating wind are those where shallow water sites are being filled with fixed structures, an example is the United Kingdom.
From about 80 meters water depth, floating wind technology can be utilized. Floating wind technology has the potential to harness wind power at greater ocean depth. Naval architecture is playing an important part in the development of floating offshore wind turbines.
ACKNOWLEDGEMENTS
Alan Crowle thanks his colleagues at the University of Exeter for their assistance in preparing this paper and in particular for the assistance of Professor PR Thies.
Author’s profile

He has a BSc in naval architecture and shipbuilding from the University of Newcastle upon Tyne (1974) and MSc in engineering for marine professionals at the University of Plymouth (2020). He has over 51 years experience, in the design, construction and offshore installation of marine structures. His work includes jackets, modules, FPSOs, semisubmersibles, loading buoys, LNG terminals and nearshore pipelines. He has renewable energy experience of fixed offshore wind turbines, met masts and high voltage direct current platforms. He is a fellow of RINA, IMAREST and SCMS
I am interest in reading about mooring FOWT during winter in a bay in Ireland awaiting a weather working installation period from April to October