Introduction
Pipes (or linepipes or joints) are used for multiple purposes and locations in the maritime/offshore industry. Onshore and offshore pipelines are used for transportation of fluids on land, over and underwater.
Pipes are fabricated in an onshore facility and they may be transported using trucks, ships, or barges to the location where they are to be installed. They may also need to be stored in the yard before they can be loaded on to trucks/ships.
How do we store pipes? Naturally, the easiest way is to stack them layer over layer, as shown in
Fig 1 below.
Figure 1: Tiers and stacking of pipes
Nested Diameter, Pipe Yield Stress and Stacking height limit
Pipes can be stacked one above another forming different tiers or ‘stacks’. The pipes of the second tier (the one just above the bottom tier) will sit in the grooves created in the bottom tier. Similarly, the third-tier pipes will sit in the grooves of the second tier and so on. If we continue like this, a trapezium-shaped stacking will be created, as shown in Figure 1 above.
Nested OD
This type of stacking is called ‘nested’ stacking (pipes sitting in grooves). With the pipes sitting in the grooves, the total height of a stack of pipes is less than the number of stacks times the diameter. This gives rise to the term ‘Nested Diameter’. Nested Outer Diameter (Nested OD) is the total height of the stack divided by the number of stacks. This is lesser than a pipe’s outer diameter.
Nested Diameter (Nested OD) = Total Height of Pipe Stack / Number of stacks
Below we will derive a simple formula for Nested OD.
In the above figure, R is radius of pipe = Pipe Outer Diameter (OD)/2.
h = vertical distance between two tiers = √3/2 x Pipe OD
If the number of tiers is n, then
Stack Height, H = R (for bottom tier lower half) + (n-1) x h + R (for top tier upper half)
H = pipe OD + (n-1) x √3/2 x pipe OD
Nested OD = H/n
Stacking Height Limit
This naturally raises a question: how high can we keep stacking pipes safely? As we keep stacking, we realize that the bottom tier of the pipe takes an increasingly higher weight. The stacking height is determined by the maximum number of stacks that we can add before the bottom tier yields. How do we measure this yielding?
- For bare pipes, the yield limit is the yield stress of steel of pipe
- For concrete pipes, either the concrete or the steel may yield. The first one to yield governs the yield limit
- For pipes with anti-corrosion coating, the coating may also yield, but it is usually not governing in comparison to steel and concrete yielding.
Let’s talk a bit more in detail about calculating the stacking limit by taking the case of bare pipes. For the bottom tier of pipes, the following loads are acting –
- Load Case 1 – Load due to pipes above
- Load Case 2 – Self-weight
These two are depicted below:
How do we calculate the value of L, the load on the bottom tier?
We can see that L is the load due to the weight of the tiers above. Hence, if the total number of tiers is ‘n’, then the load of the tiers above is L = (n -1) x w, where w is the weight per unit length of the pipe. This load comes onto the bottom pipe from the two pipes above at angle 30 degrees to the vertical.
Thus L = 2P cos 30. This gives P = L/ (2 cos30) = (n-1) x w/ (2 cos30)
From Roark’s formula, the maximum moment which the pipes are subjected to due to the first load case is M1 = 0.5106 PR (See Table 9.2, Case 5, KMC = 0.5106). R is the pipe radius
Thus, the moment from the first load case,
M1 = 0.2948 (n-1) wR
The second load on the pipe is the self-weight, which gives as per Roark’s formula (Table 9.2, Case 15),
M2 = 1.5{w/(2πR)}R2 = 0.2387wR
Combining the two moments, we get
Total moment on the bottom pipe, M = M1 + M2 = (0.2948n – 0.0561)wR
The bending stress is calculated as,
Bending Stress on pipe = Bending Moment/ Section modulus of pipe for transverse bending.
Section modulus for transverse bending = t2/6, where ‘t’ is the pipe thickness
This gives the bending stress as
σBEND = M/Z = (n – 0.1903)wR/(0.5654t2)
If the allowable bending stress is σALLOW, then σBEND has to be less than σALLOW. From this, we get
n < 0.5654 σallowt2/wR + 0.1903
From the above in-equality, we can see that the number of tiers has to be less than 0.5654 σallowt2/wR + 0.1903.
Once we know the maximum number of tiers that can be stacked, we can use the formulas specified before to calculate the stacking height and nested OD
H = pipe OD + (n-1) x √3/2 x pipe OD
Nested OD = H/n
Thus, by using simple principles of force resolution and basic stress calculations, we can find out how many tiers of a particular pipe type can be stacked up, and to what height.
For subsea pipelay operations, multiple pipe types may be present with varying properties. The stacking height of each of them can be calculated using this principle.
Disclaimer: This post is not meant to be authoritative writing on the topic presented. thenavalarch bears no responsibility for the accuracy of this article, or for any incidents/losses arising due to the use of the information in this article in any operation. It is recommended to seek professional advice before executing any activity which draws on information mentioned in this post. All the figures, drawings, and pictures are property of thenavalarch except where indicated, and may not be copied or distributed without permission.
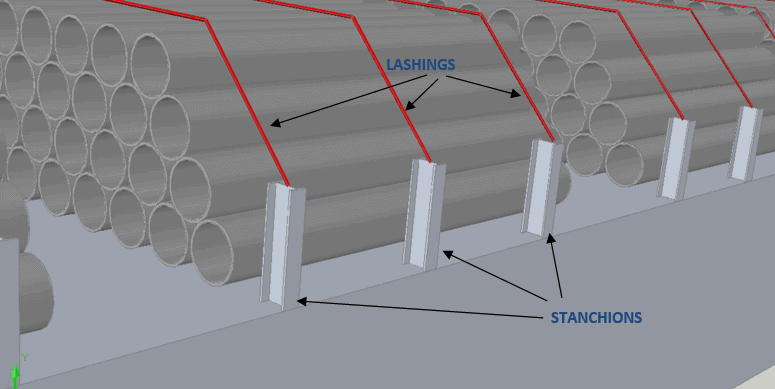
Introduction to Pipe Transportation – Part 3 (Engineering)
Introduction to Pipe Transportation - EngineeringIn Part 1 we learnt about pipes, while in Part 2 we learnt about Planning and Scheduling of pipe transport operations. In this part, we will learn about Engineering.Phase 3 – Engineering.Engineering for pipe...

Introduction to Pipe Transportation – Part 2 (Planning & Scheduling)
In Part 1, we looked at the properties of pipes. In this section, we will be looking at the Planning & Scheduling of a pipe transportation operation (see below, Phase 1 & 2) SECTION 2: PLANNING, SCHEDULING, AND ENGINEERING FOR A PIPE TRANSPORT PROJECT Source:...
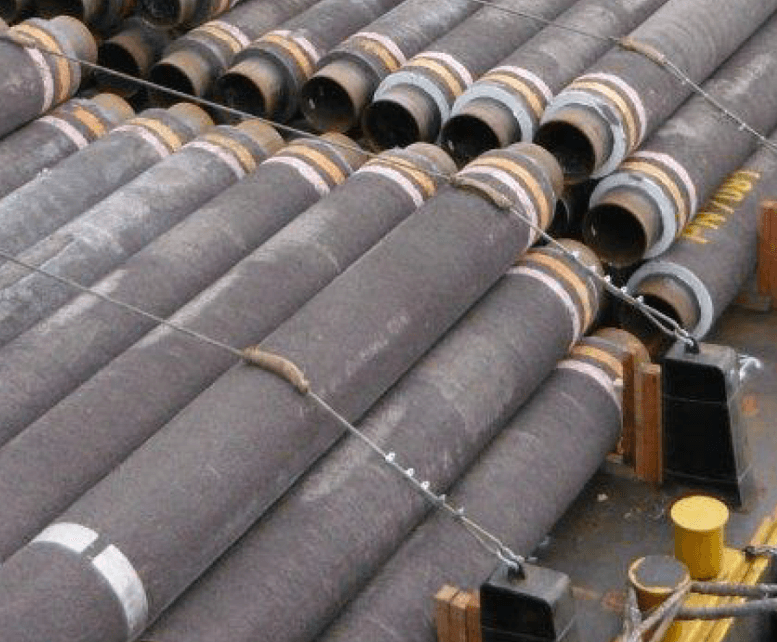
Pipe Transportation – An Introduction (Part 1)
(To read Part 2, click here) This is the first part in the 3-part series on Pipe Transportation. In this part we will discuss about pipes and their properties. In this article, we will talk about the transportation of pipes on ships. Pipes are needed for various...
i need a help with the plan on stacking of storm water pipes
Hi Rose
Thanks for the inquiry. Sent you an email
Hi,
May I know the height limit if:
OD = 90cm
length = 5m
Weight = 400kgs
Thank you.
I need a help with with the plan on stacking of Casing different Sizes.
Hi Sain
Can you write with more details to us at info@thenavalarch.com? Thanks
Steel pipe loading on ship calculation
Looking for recommended calculations for pipe stacking in bridge configuration. Thanks
What is formula of the Lashing Calculate ondeck load cargo
Hi Yasar, you can do it based on IMO CSS. If you need help in doing it, feel free to write to us at info@thenavalarch.com
what is the maximum height/tier for stacking of pipes of various diameter/sizes