Introduction
Chocks are used universally for mooring and towing operations on ships.
For towing operations, Chocks are used for guiding the towing rope from the winch through the outer shell of the vessel to the tug. For mooring operations, the chock is used to guide the mooring rope from bollard/bitt on the deck of the vessel through the outer shell of the vessel to the mooring points on the jetty/pier/quay. A typical closed chock design looks like the below:
The closed chock has a body which is round in shape and it has a rectangular shaped seating that is welded to the deck of the vessel.
This article talks about designing a closed chock as per the relevant requirement of the International Association of Classification Societies (IACS) rules. The guiding rule followed is the Unified Requirement (UR) A2 Rev 5 (Sep 2020).
In this article we’ll see what kind of forces are expected on a chock, and what design stresses we need to evaluate it for, to check its suitability for an operation.
Design Load
The design load on a chock will depend on the purpose the chock is deployed for.
When the chock is used for towing, there are two scenarios of towing that UR A2 covers:
- Normal towing operations: this relates to towing in ports and sheltered waters
- Other towing operations: to assist the ship in case of emergency as given in SOLAS Regulation II-1/3-4 Paragraph 2.
During normal towing operations, the force on the chock comes from the load on the towline that connects the vessel to the tug pulling it. The maximum bollard pull of the tug will be the governing load on the chock. During emergency (other) towing operations, the governing force becomes the Ship’s Design Maximum Breaking Load as defined in UR A2 thus:
Ship Design Minimum Breaking Load (MBLSD) means the minimum breaking load of
new, dry mooring lines or tow line for which shipboard fittings and supporting hull
structures are designed in order to meet mooring restraint requirements or the towing
requirements of other towing service.
If the chock is used for mooring, then the loads on the mooring lines will be the governing loads. In this case, the Ship’s Design Maximum Breaking Load (SDMBL) is taken as the design load for mooring loads on the ship’s fittings.
Load Cases
The chock can be subject to different load cases, depending on the angle at which the design load is acting on the chock.
The design load (DL) is the load acting on the towing/mooring line.
The next question is: at what angle these forces should be considered on the chock?
Case 1: Angle in the horizontal plane
The chock’s purpose is to guide the line from winch/bollard to the pier/tug. This will result in the line making an angle around the chock’s inner surface as shown below. The angle(θ) depends upon the position of the winch/bollard and the position of the pier/tug. This angle may vary depending on the use case, and so a conservative minimum angle should be used for design.
In case the determination of this angle is not feasible, it is taken as zero. Depending on the angle input, the effective (resultant) load on the chock can be calculated as follows:
F (resultant load on chock) = 2 x DL x cos(θ), see figure below
Design load and angle on the chock (source: IACS UR A2, A.2.1.3)
We can see that if we take θ as zero, the resultant force on the chock F becomes 2 x DL, and this represents a worst-case scenario. If a reliable assessment of θ is not available, we should take F = 2 x DL.
Case 2: Angle in the vertical plane
The previous loading case had the force F in the horizontal plane. There’s another possibility of loading when the line from the bollard/winch on the deck and through the chock goes vertically down, thus resulting in the force in the vertical plane. This scenario is depicted below.
A force diagram on the chock will look like the below:
Here, we can see the design load on the line (DL) acts as Tx and Ty in the horizontal and vertical directions on the chock.
Stress Checks
Once the loading conditions are established, the next will be the stress checks for the chock structure.
The stress check will include the following for each load case:
- Bending Stress Check on the Chock
- Shear Stress due to horizontal component of load
- Axial stress due to vertical component of the load
- Normal stress check (bending + axial)
- Shear, tensile, bending and total stress on the weld between chock and chock seating
The same set of stress checks will also have to be performed for the chock seating which connects the chock to the deck of the vessel. The weld between the seating and deck will also need to be checked for all the applicable stresses.
Once stress checks are done and the chock design verified, the chock can be considered fit for the purpose it’s built for.
Disclaimer: This post is not meant to be authoritative writing on the topic presented. thenavalarch bears no responsibility for the accuracy of this article, or for any incidents/losses arising due to the use of the information in this article in any operation. It is recommended to seek professional advice before executing any activity which draws on information mentioned in this post. All the figures, drawings, and pictures are property of thenavalarch except where indicated, and may not be copied or distributed without permission.
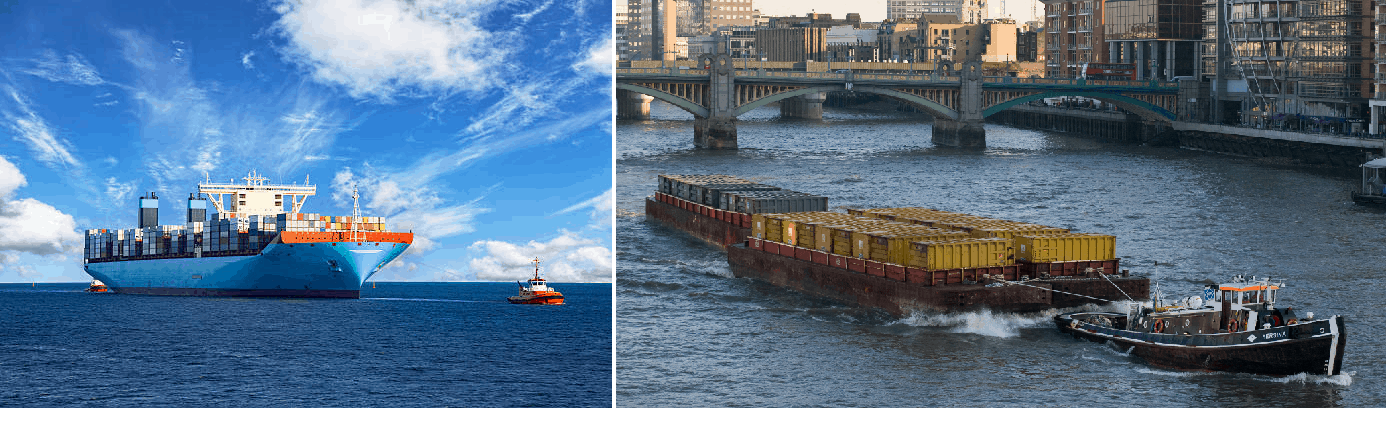
Why the bollard pull calculation method for a barge won’t work for a ship
In my working with the marine transportation industry for more than a decade now, I have come across many different calculations for required bollard pull for both barges and ships. The principles of the calculation are same, whether it is a ship, a barge...
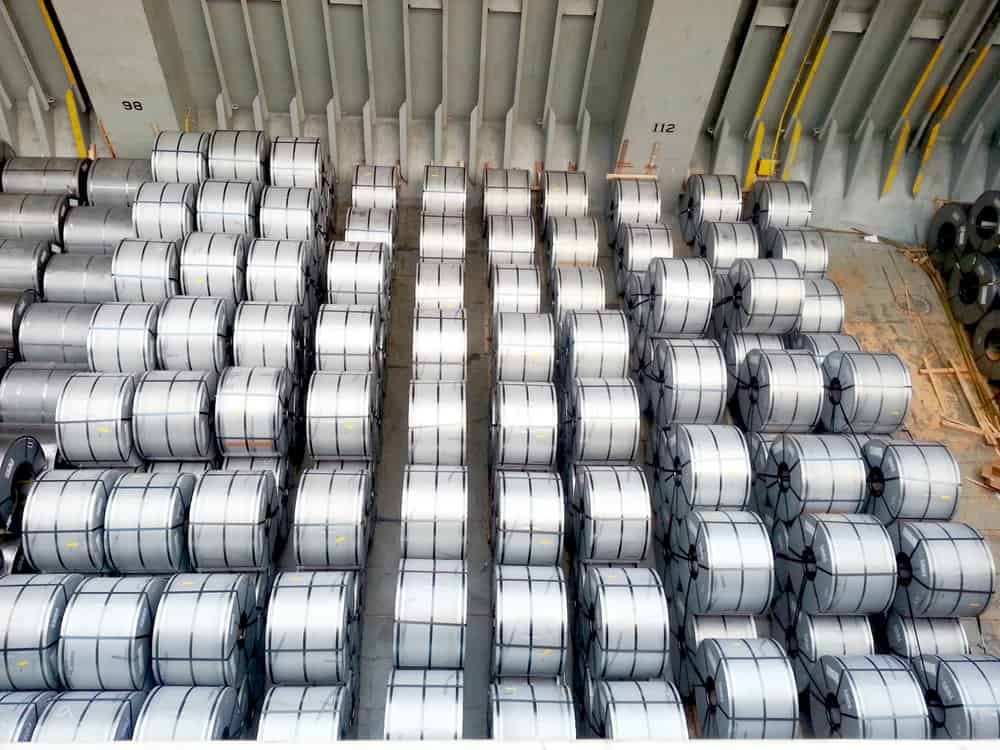
STEEL COILS LOADING – ITS CHALLENGES AND WAYS TO OVERCOME
STEEL COILS LOADING – ITS CHALLENGES AND WAYS TO OVERCOME by Mr. Spiros Malliaroudakis (Founder & Managing Director, S.A. Malliaroudakis Maritime (UK) Ltd) The loads derived from steel coils loading are very concentrated, leading to higher stresses...
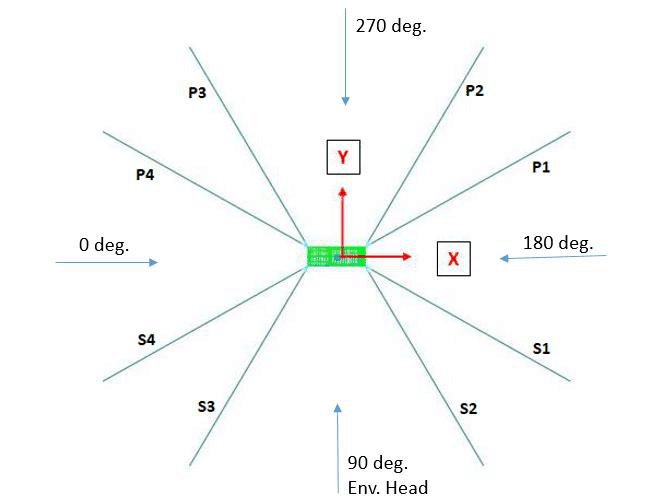
Mooring System Design and Analysis
Mooring System Design and Analysis by Rahul Kanotra, Consultant Naval Architect As the offshore industry moves towards greater technological advancements, one thing that has plagued the engineers is the “plug and play” computer programs or software. I am not against...
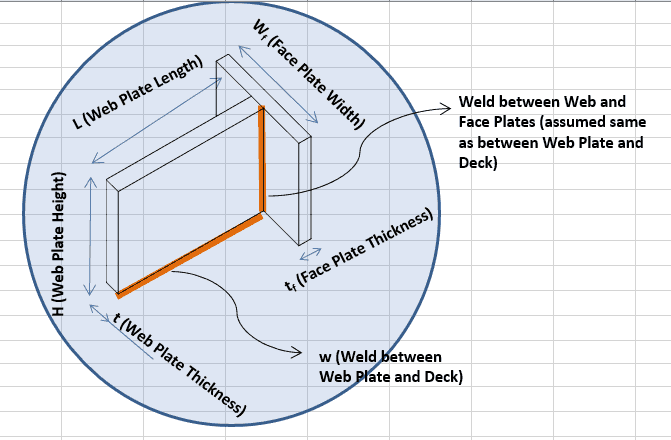
Cargo Stoppers – why they are critical and how to design them
Stoppers and their critical role in seafastening of cargo Introduction A cargo transported on the deck of a ship is subject to many forces. These forces comprise of the inertial forces due to the ship motions – the three translations and three rotations – and the...
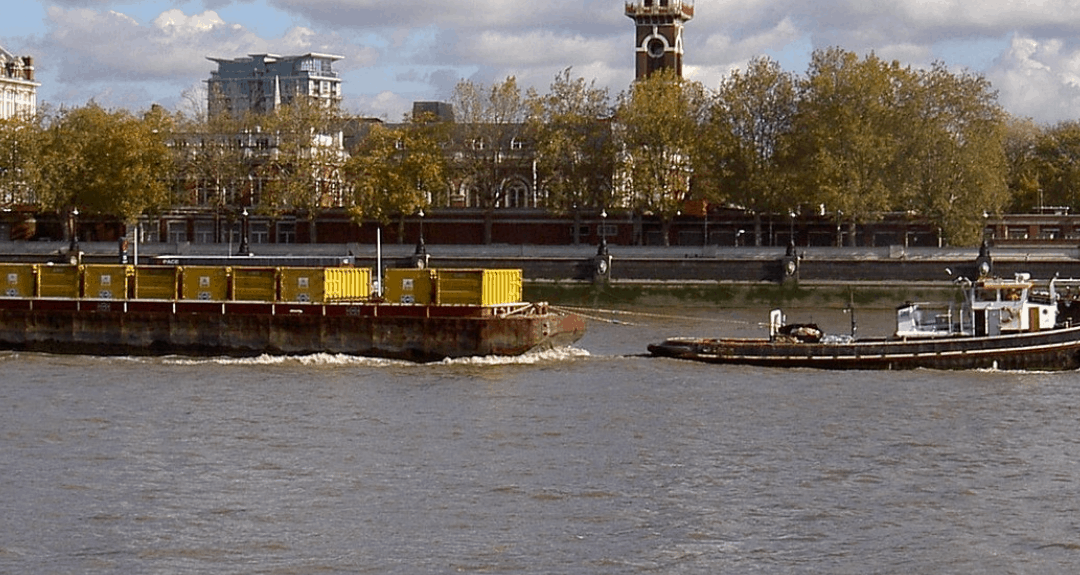
Are you chartering a tug bigger than necessary for your Barge?
Barges are one of the most frequently used means for transporting deck cargo of different shape, size and weight. While some barges are self-propelled, the majority is towed by another vessel called a ‘Tug’. Once an owner or charterer...
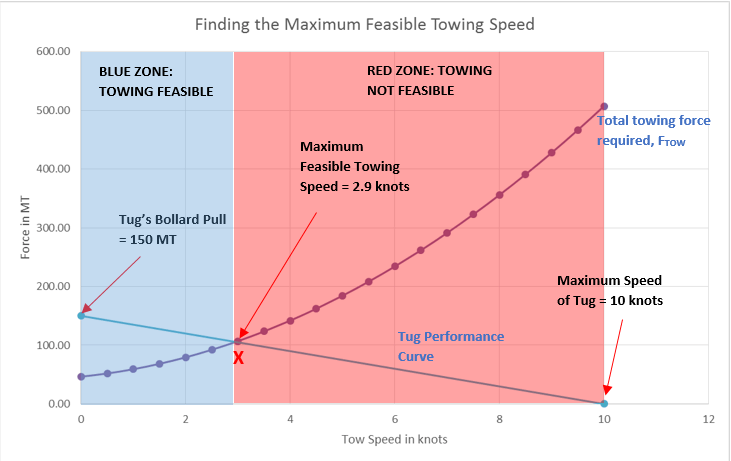
Bollard Pull Calculations – an Introduction (Part II)
Bollard Pull Calculations for Towing Operations Part II - Finding out the maximum feasible tow speed (To read Part I, please click here) Introduction This is Part - II of the two part article on Bollard Pull calculations. In the Part I we saw how to calculate the...
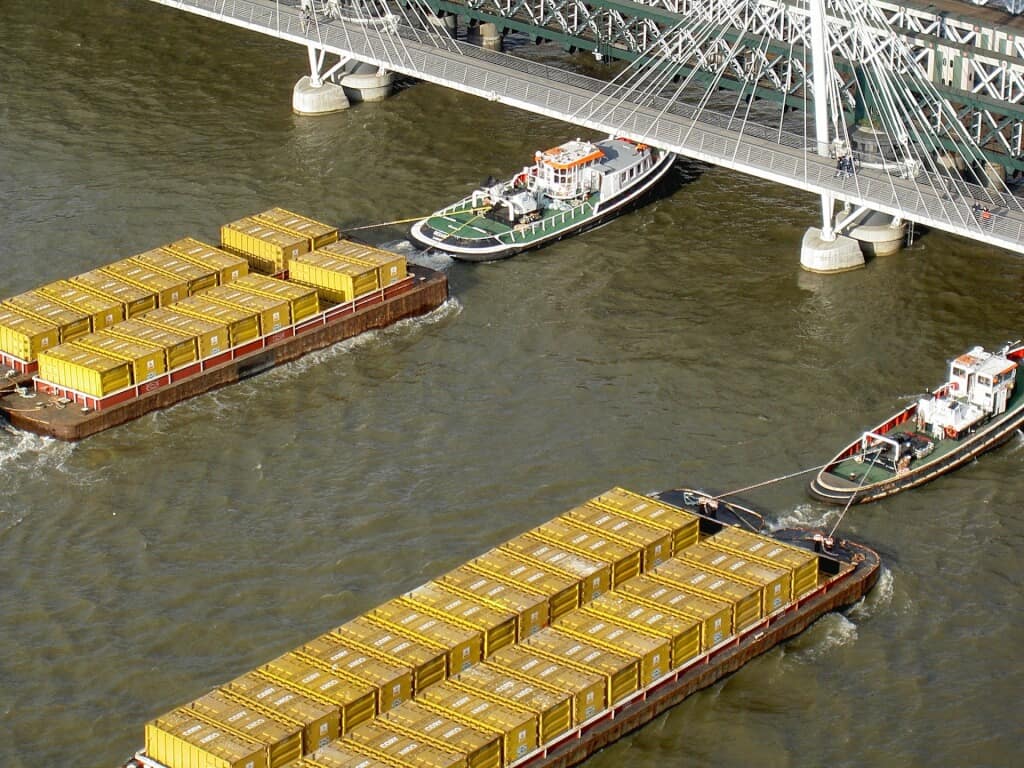
Bollard Pull Calculations – an Introduction (Part I)
Bollard Pull calculation is one of the most frequent calculations performed in marine towing operations. Towing operations involve the pulling of a vessel (it can be a barge, ship or an offshore structure) using another vessel (usually a tug).
Please check out TheNavalArch’s product for IACS chock design:
Send me some info.
Need the design calculation for designing chock