Introduction
GRP laminates are widely used in the fabrication of high-speed crafts and light crafts/boats globally. GRP stands for Glass Reinforced Plastic. As the name suggests, GRP contains glass fibers embedded into a plastic resin. This gives it higher strength, durability, and also a smooth finish [Ref 3].
A laminate used for the fabrication of boats will usually have multiple layers of reinforcements of GRP to achieve the desired strength. In this article, we will learn about a method to calculate the desired number of layers of laminate reinforcements to be used to attain a desired thickness of the laminate. The article follows the formulations provided in the Indian Register of Shipping, Rules and Regulations for the Construction and Classification of High-Speed Crafts and Light Crafts Chapter 7 General Hull Requirements for Fiber Composite and Sandwich Constructions, Section 5 Material Properties and Testing.
CSM vs Woven Roving
There are two major types of GRPs used in boat fabrication. The first one is CSM, short for Chopped Strand Mat. The CSM has random fiberglass of various lengths dispersed through the resin to provide equal distribution in all directions. Woven Roving, on the other hand, resembles a cloth with woven strands of fibers to form a lattice pattern (see fig below)
CSM vs Woven Roving
Application to FRP boats
FRP, or Fiber Reinforced Plastic boats are made from laminates which have multiple layers of either Woven Roving (WR) or Chopped Strand Mat (CSM), or a combination of the two. The resulting laminate must have the requisite strength and other material properties suitable for its purpose.
How thick the laminate should be? The minimum thickness is provided in the rules of Classification Society to which the boat is classed. Since the laminate is made of multiple layers of reinforcements of CSM or WR, it is important to be able to select the right number of layers of CSM or WR to be able to attain the requisite thickness of the laminate.
Hence, if
- nCSM is the number of layers of CSM with the thickness of each CSM layer being tCSM, and
- nWR is the number of layers of WR with the thickness of each WR layer being tWR, and
- tREQ is the required thickness of the laminate, then
tREQ = nCSM x tCSM + nWR x tWR
Properties of WR and CSM
Since glass is an integral part of the reinforcement layer, the properties like the strength of the laminate are expected to be dependent on the amount of glass reinforcement in the laminate layer.
WR and CSM differ in their mechanical properties owing to the difference in their structure. The tables below demonstrate the difference in their properties
We can note from the tables above that the property GC is central to calculating all the properties of the laminate layer. GC is the Glass Content Ratio by weight of reinforcement within the laminate. Thus the calculation of GC is a pre-requisite to the calculation of the laminate layer’s properties.
Thickness calculation for the laminate
Now we come to the next stage – how to calculate the number of WR or CSM layers needed to achieve a desired thickness?
For this, we will refer to a formula from the Indian Register of Shipping rules [Ref 1]. The formula calculates the thickness of the ith laminate layer from two properties:
- Weight of reinforcement of the layer (expressed in g/m2), Wi
- The Glass Content Ratio, GC, explained above
The formula is shown below:
We can see that the total thickness is the sum of the thicknesses of individual layers. The thickness of the ith layer is given by
ti = wi/3072 x (2.56/GC – 1.36), in mm
The layers of the laminate can be made up of WR or CSM or a combination of both. We can achieve a target thickness by trying out different types and numbers of CSM and WR layers, calculating their individual thicknesses and adding them up to check if the minimum thickness (as prescribed by Class rules) is being achieved.
The material properties of each layer can also be calculated using the value of GC for the layer. The material properties of the entire laminate then can be calculated as a thickness-averaged value for all layers.
For example, the ultimate tensile strength (SU) can be calculated thus:
SU = Σ (Sui x ti)/Σ(ti)
Looking at the above calculations, a spreadsheet solution can be set up for performing the calculations in the following steps:
- Step 1 – calculate the required thickness of the laminate from Class Rules
- Step 2 – add multiple rows in a spreadsheet, each row representing a laminate layer which can be either a WR or CSM.
- Step 3 – keep adding rows of laminate layers and calculate their individual properties (thickness and other properties), at the same time calculating the cumulative properties of the laminate.
- Step 4 – The required number of layers is obtained when the target thickness of the laminate is reached
From the steps above, an optimum number of laminate layers required can be obtained. Ending up with a thinner laminate means weaker laminate and thicker laminate means excess material is being spent, and this method can provide the optimum.
TheNavalArch has developed its own app that can be used to calculate the optimum number of layers required for a laminate of requisite thickness. Please do spend some time to check it out
References
- INDIAN REGISTER OF SHIPPING – Rules and Regulations for the Construction and Classification of High Speed Crafts and Light Crafts, Chapter 7 General Hull Requirements for Fibre Composite and Sandwich Constructions, Section 5 Material Properties and Testing
Disclaimer: This post is not meant to be authoritative writing on the topic presented. thenavalarch bears no responsibility for the accuracy of this article, or for any incidents/losses arising due to the use of the information in this article in any operation. It is recommended to seek professional advice before executing any activity which draws on information mentioned in this post. All the figures, drawings, and pictures are property of thenavalarch except where indicated, and may not be copied or distributed without permission.
TheNavalArch Interview Series: Mr. Balakrishna Menon
Mr. Balakrishna MenonEngineering Director Mooreast (Asia) Pte Ltd TheNavalArch's Interview Series is an endeavor to get insights from the best engineering and business brains in the industry, and present them to its users for the larger...
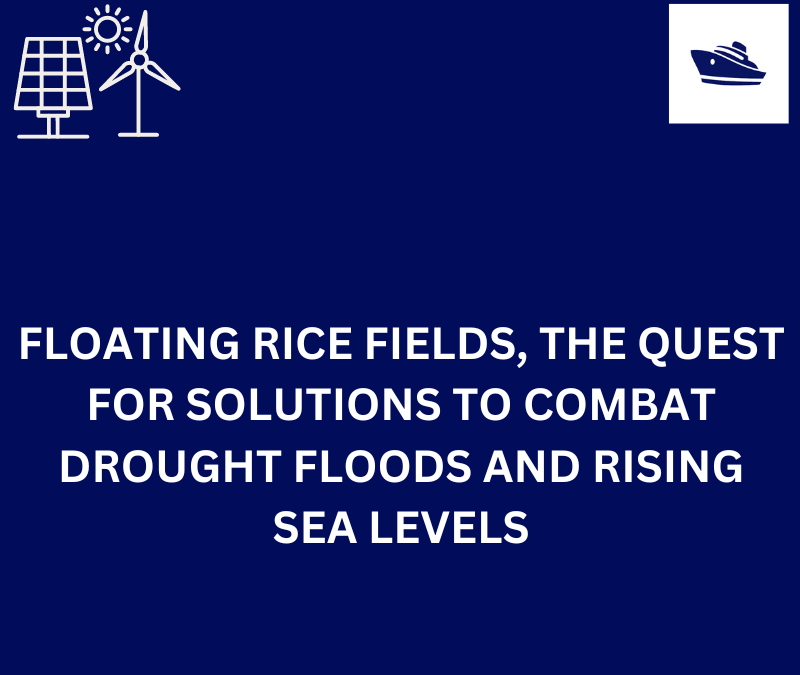
Floating Rice Fields, the quest for solutions to combat drought floods and rising sea levels
by Lim Soon Heng, BE, PE, FSSS, FIMarEST Founder President, Society of FLOATING SOLUTIONS (Singapore) Abstract Amazing as it seems, there is a case for growing rice on floating platforms in the sea. The capital expenditure to develop this is offset by the opportunity...
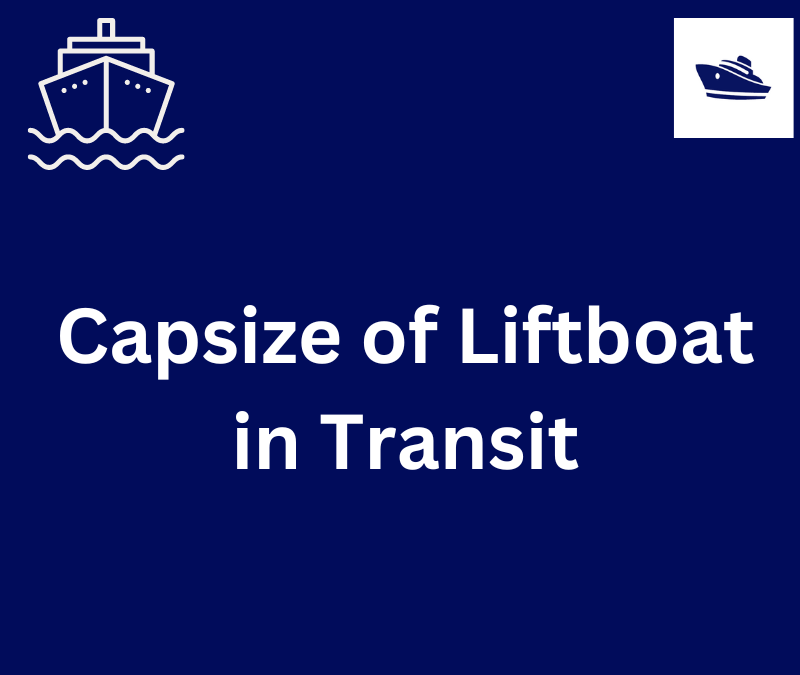
CAPSIZE OF LIFTBOAT IN TRANSIT
This paper was originally presented in the 27th Offshore Symposium, February 22nd, 2022, Houston, Texas Texas Section of the Society of Naval Architects and Marine Engineers It has been reproduced here for the readers of TheNavalarch INTRODUCTION In 1989 a Class 105...
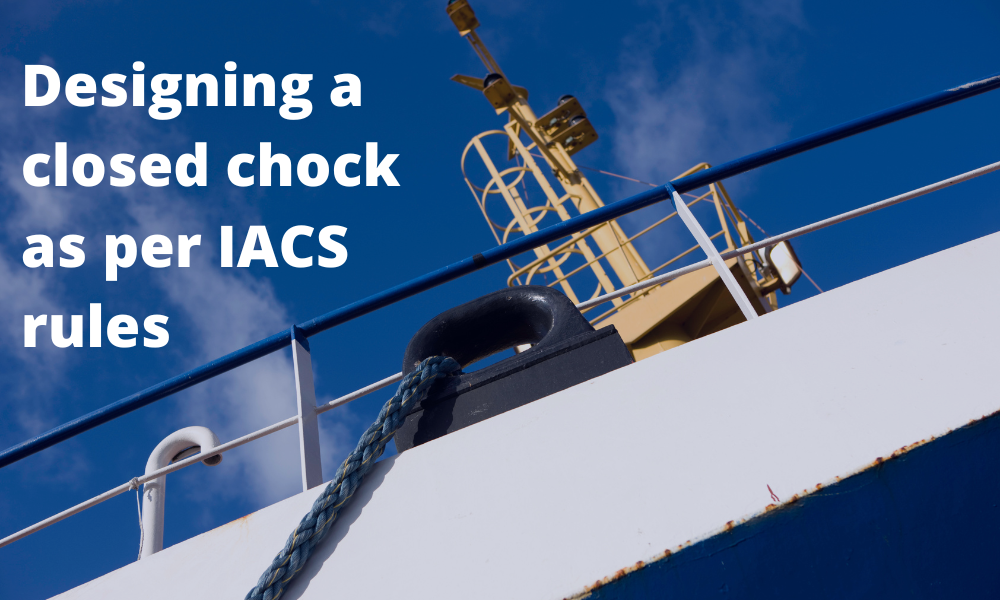
Designing a closed chock as per IACS rules
Introduction Chocks are used universally for mooring and towing operations on ships. For towing operations, Chocks are used for guiding the towing rope from the winch through the outer shell of the vessel to the tug. For mooring operations, the chock is used to...
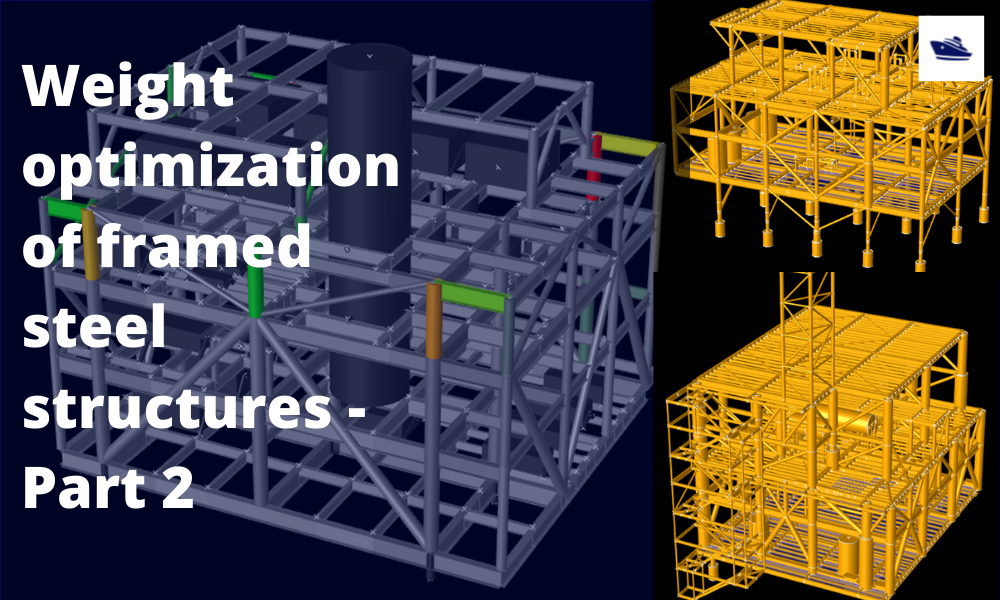
The Optim22 method of hull optimization – Part 2
This is a follow-up article to the previous article on Framed Structures Optimization. 1.1 Abstract A previous article introduced the Optim22 method. This one adds additional background information plus 3 more case studies to...
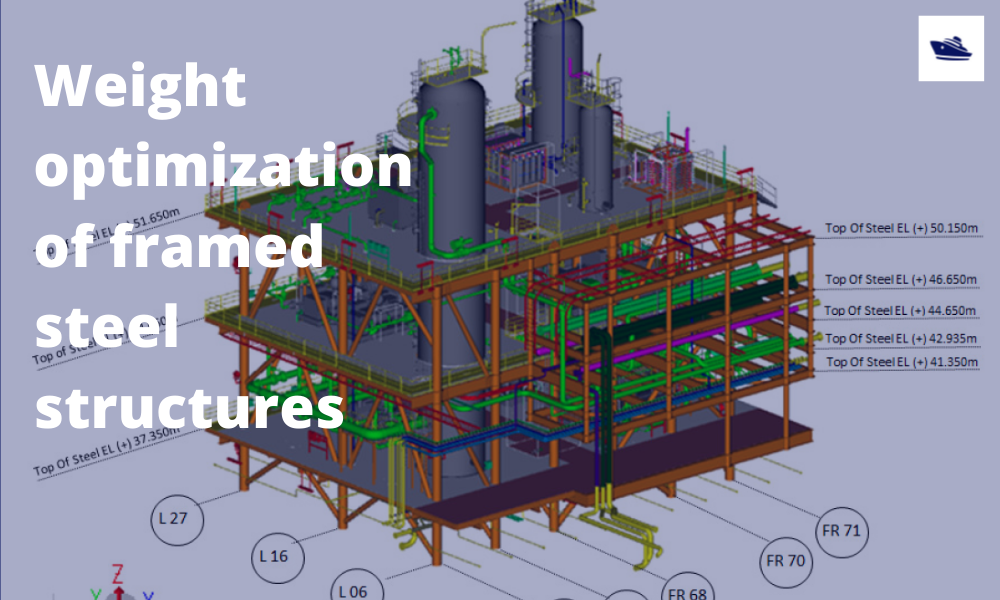
The Optim22 Method of Weight Optimization of Framed Steel Structures
1 Abstract A semi-automated structural weight optimization system is presented for framed structures of post and beam construction which is based on basic structural member design principles. The approach is to adjust member properties in a manner that...
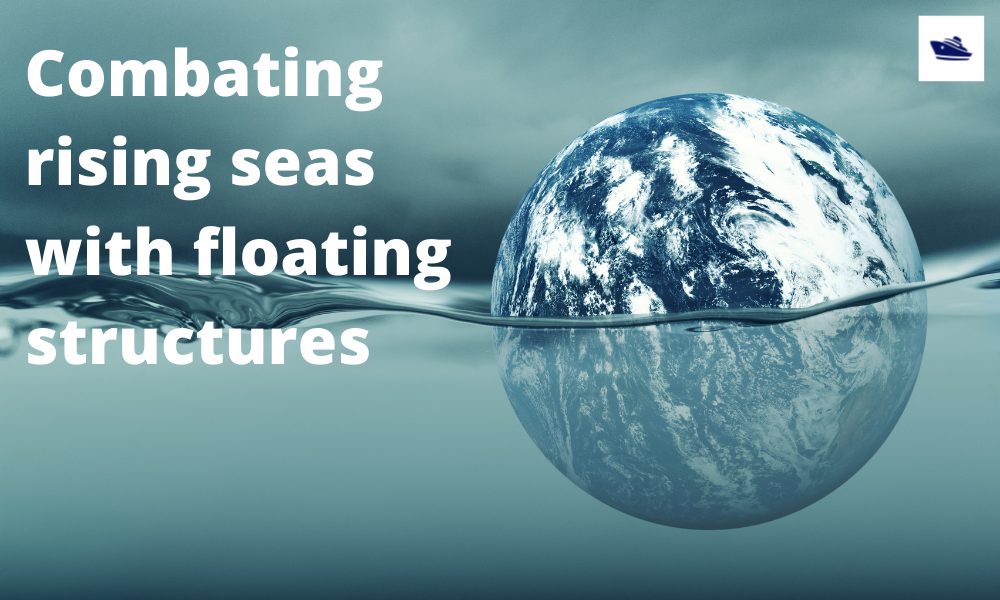
Combating rising seas with floating structures
Introduction Rising sea level is an existential threat for many coastal cities. The sea is rising subtly but relentlessly at an exponential rate. Many predictions of how high and how fast it will rise in the next 50 years have proved to be understated. According to...
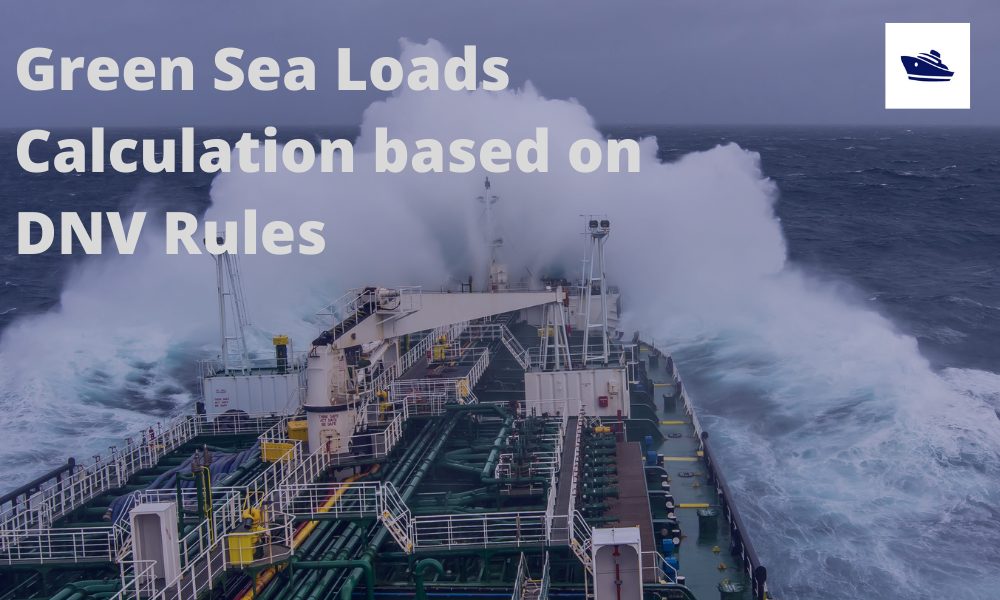
Sea Pressure Loads Calculation based on DNV Rules
Introduction Sea pressure loads are an important factor in the structural design of a vessel. What is sea pressure load? As the term suggests, it is the external pressure on the vessel due to the surrounding sea. What kind of pressure it is, and how to...
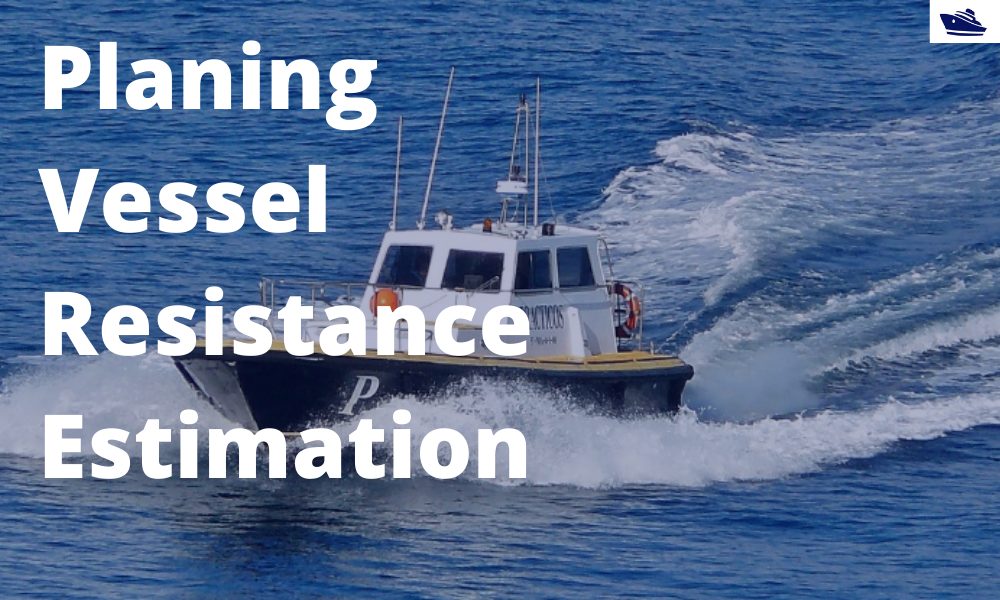
A quick empirical method for resistance estimation of planing vessels
Resistance estimation for a vessel is a fundamental exercise in design of the vessel. Resistance is a property that depends on the vessel’s shape and form. A conventional ship-shaped vessel with a bulb will have completely different resistance characteristics compared...
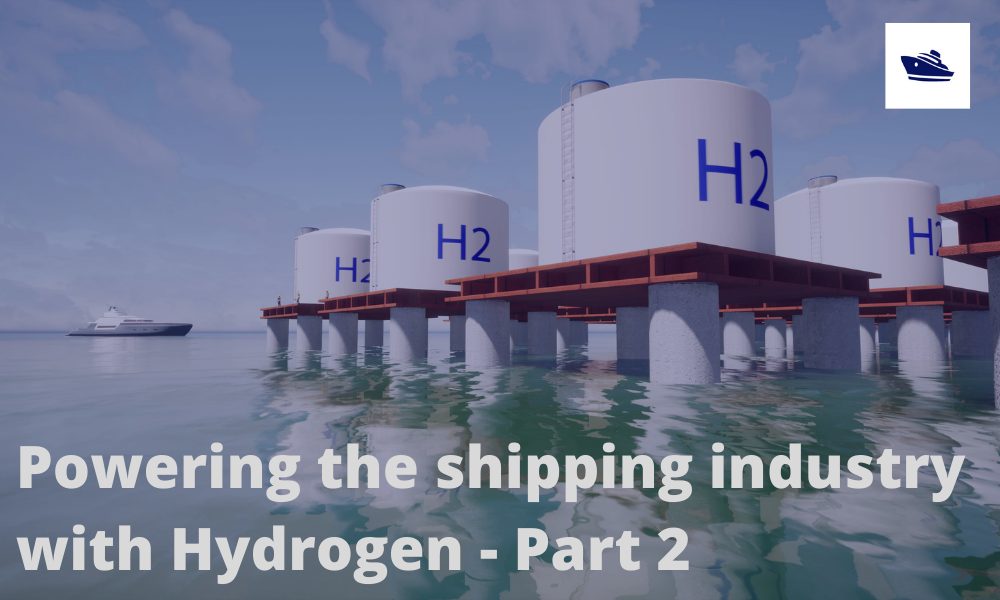
Powering the maritime industry with Hydrogen – Part 2
Powering the shipping industry with hydrogen - Part 2: Hydrogen propulsion on a ship - opportunities and challenges Introduction In the Part 1 of this article, we explored the basic properties of Hydrogen as a fuel, and also the opportunities and challenges...
Thanks