In the offshore construction industry, the connection between the newly installed pipeline and the riser is accomplished via a series of ‘spoolpieces’ (or spools). The spool is fabricated by welding pipe joints to form an L–shaped, Z–shaped, or possibly a straight pipe. The figure below shows that four spools connect the riser flange to the pipeline flange, where the first, second, and fourth spools are L-shaped, whereas the third one is a straight spool.
The lifting analysis of a subsea spoolpiece typically yields the specifications of the lifting slings and the lifting configuration, which represents the location of the pick-up (rigging) points. In addition, the analysis checks the stresses in the spools resulting from the lifting forces. However, the pipe stresses would be of concern in limited cases where we have to use a small lifting angle (with the horizontal), and the bend angle is approximately 90 degrees, coupled with a small pipe (e.g., 8 inches or less). Otherwise, lifting the spool does not usually cause stresses exceeding the allowable limits.
In all cases, we must obtain the lifting configuration; thus the tension in the wires, to correctly choose the suitable slings. That means we must find/purchase the slings matching the analysis results, which may cost much. However, the main problem is the potential delay of providing the slings if we have a tight schedule, e.g., when changing the lifting configuration of the closing tie-in spoolpiece.
What if the lengths of the available slings become an input in the analysis procedure? In other words, the question becomes, “where can I install a sling of a particular length on the spool, with a particular hook height?” So if we were able to change the way we do the analysis, we would be using slings available in the stock, provided they have reasonable sizes and lengths, saving costs in many ways. Is that possible?
The answer is yes. The basic idea of obtaining the location of the pick-up points is that they represent the intersection between a sphere and a straight line, but how?
The sphere is centered at the hooking point, and its radius is the sling length. That means that the sphere surface represents all the possible points in space around the hooking point that are at an equal distance of the sling length from it. These points, of course, include the pick-up points we are looking for; thus, our job now is to find the intersection points between the sphere and the spool straight lines. See the below illustrating sketch.
Mathematically speaking, the sphere equation is defined by the center (hooking point) and the radius (sling length). And of course, the hooking point should be at a suitable vertical distance (hooking height) from the center of gravity, which should be calculated as well. Of course, that hook height should be reasonably shorter than the shortest sling. On the other hand, the spool equation is identified by the spool pipes lengths and bends’ angles. Consequently, the two equations must be solved simultaneously, yielding, ideally, two quadratic the root(s), representing the coordinates of the pick-up points of one particular sling length on a specific spool pipe.
Furthermore, the tension in the slings can be found by simple equilibrium equations of rigid body mechanics. So we have six equilibrium equations: three for summing forces in the three coordinate directions and three for summing moments. In that case, if we imagine that the max number of slings is six (which is practically too many), we can use as many equations as the number of slings we wish to use. Ultimately, we solve these equations simultaneously, get the tension, and subsequently choose the proper slings or probably check if the tension matches the slings we have in stock.
This procedure can be done by Excel VBA. A program has been developed (link at the bottom of this article) that performs the whole process from identifying the center of gravity, getting the pick-up points, and obtaining the tension. And, of course, the user can redistribute the slings and get new tension values if he wishes. Obtaining positive tension values is a sign that the slings distribution is physically possible and stable.
The following video explains the concept graphically.
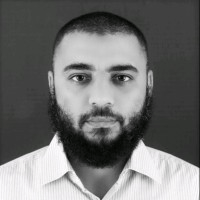
Mohamed Hermas
Founder, Offshore Engineering Guide
Mohamed is an Offshore Pipeline Engineer and a CAE specialist, holding an M.Sc. in Subsea Engineering from the University of Aberdeen. He has been working in the offshore construction industry, with a focus on pipelines and cables, for 19 years.
Hermas has served in several capacities over the course of his career. He began as a field engineer, then project engineer, installation engineer, and pipeline engineer in many places worldwide.
In 2016, Mohamed was awarded the Chartered Engineer title from the Institution of Mechanical Engineers. In the same year, he launched a website for offshore construction professionals, with the following address: offshoreengineerguide.com
Mohamed’s interest in studying the finite element method began in 2017. By 2018, he has built his first mathematical model for stress analysis by Matlab language. Subsequently, he developed solvers serving many engineering purposes using Matlab, Wolfram language, and Excel VBA. He helps companies and individuals to make tailored programs/calculators for different engineering applications for which there is no software package available in the market.
Disclaimer:
The views, information, or opinions expressed in this article are solely those of the author and do not necessarily represent those of TheNavalArch Pte Ltd and its employees
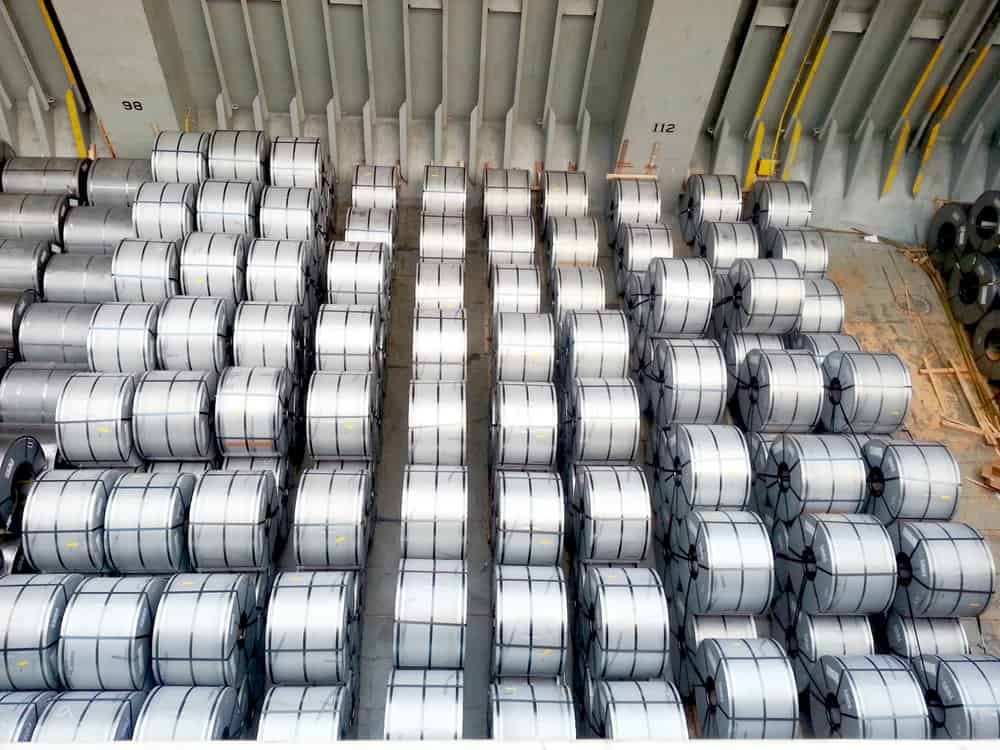
STEEL COILS LOADING – ITS CHALLENGES AND WAYS TO OVERCOME
STEEL COILS LOADING – ITS CHALLENGES AND WAYS TO OVERCOME by Mr. Spiros Malliaroudakis (Founder & Managing Director, S.A. Malliaroudakis Maritime (UK) Ltd) The loads derived from steel coils loading are very concentrated, leading to higher stresses...
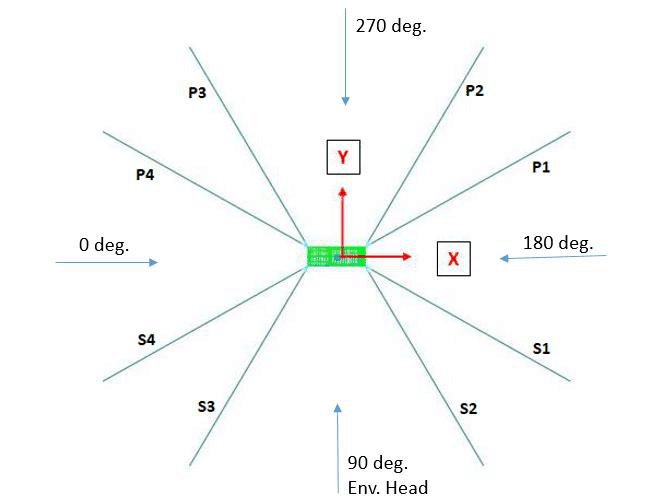
Mooring System Design and Analysis
Mooring System Design and Analysis by Rahul Kanotra, Consultant Naval Architect As the offshore industry moves towards greater technological advancements, one thing that has plagued the engineers is the “plug and play” computer programs or software. I am not against...
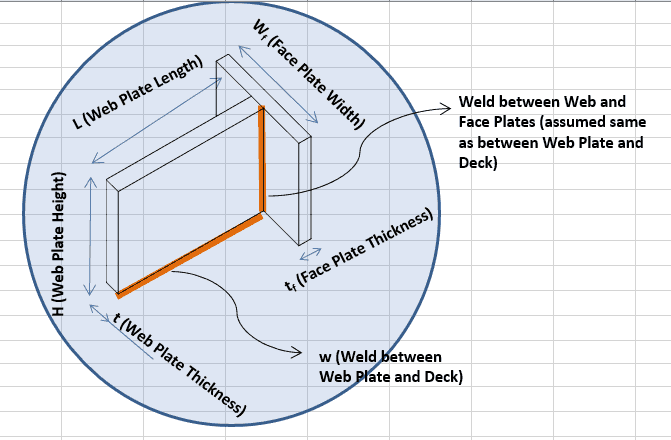
Cargo Stoppers – why they are critical and how to design them
Stoppers and their critical role in seafastening of cargo Introduction A cargo transported on the deck of a ship is subject to many forces. These forces comprise of the inertial forces due to the ship motions – the three translations and three rotations – and the...
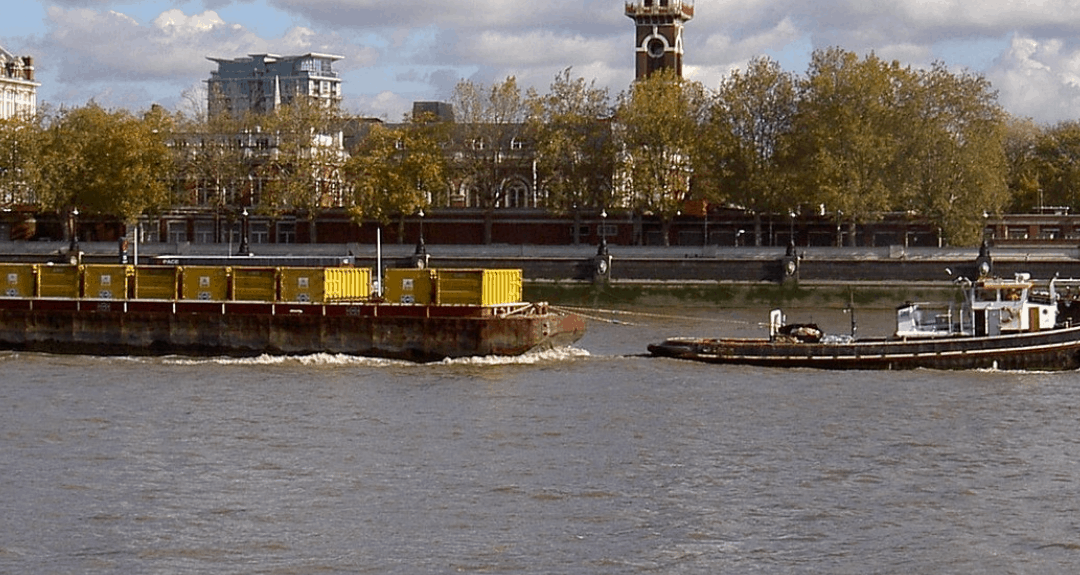
Are you chartering a tug bigger than necessary for your Barge?
Barges are one of the most frequently used means for transporting deck cargo of different shape, size and weight. While some barges are self-propelled, the majority is towed by another vessel called a ‘Tug’. Once an owner or charterer...
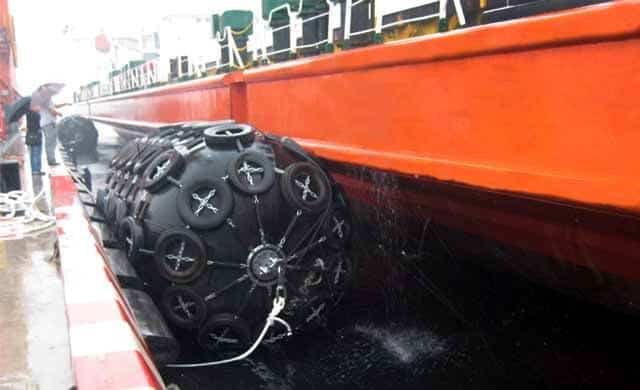
Fendering – an Introduction
In this two part article we will talk about Fendering, which is one of the basic but critical operations related to a ship. Fendering is, basically, protecting the ship’s sides from contact with another body (which can be another ship, jetty or quay wall). It can also...
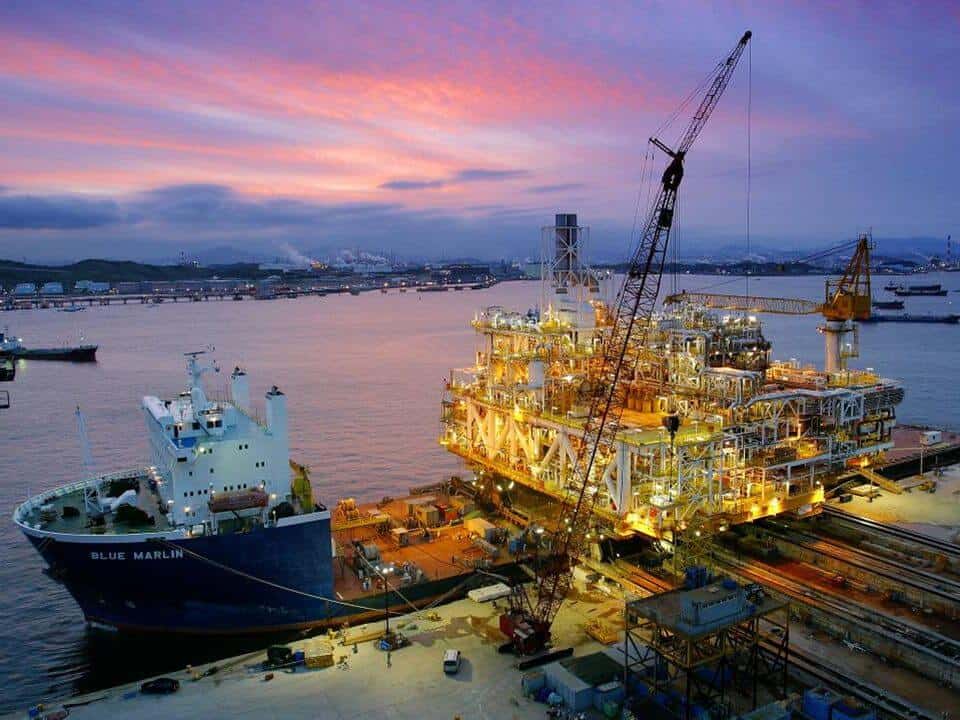
Loadouts – An introduction
Image source: Flickr Loadout Operations - an Introduction Loadout is a term oft heard of in the marine/offshore industry parlance. Loadout is generally referred to the operation of transferring a Cargo or a Structure from the place of fabrication to a sea-borne...
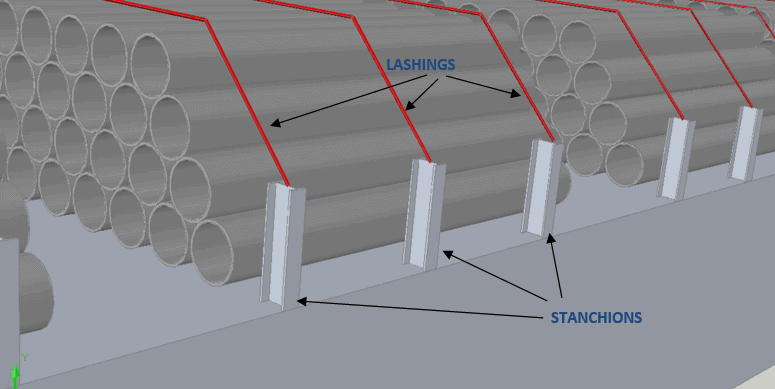
Introduction to Pipe Transportation – Part 3 (Engineering)
Introduction to Pipe Transportation - EngineeringIn Part 1 we learnt about pipes, while in Part 2 we learnt about Planning and Scheduling of pipe transport operations. In this part, we will learn about Engineering.Phase 3 – Engineering.Engineering for pipe...

Introduction to Pipe Transportation – Part 2 (Planning & Scheduling)
In Part 1, we looked at the properties of pipes. In this section, we will be looking at the Planning & Scheduling of a pipe transportation operation (see below, Phase 1 & 2) SECTION 2: PLANNING, SCHEDULING, AND ENGINEERING FOR A PIPE TRANSPORT PROJECT Source:...
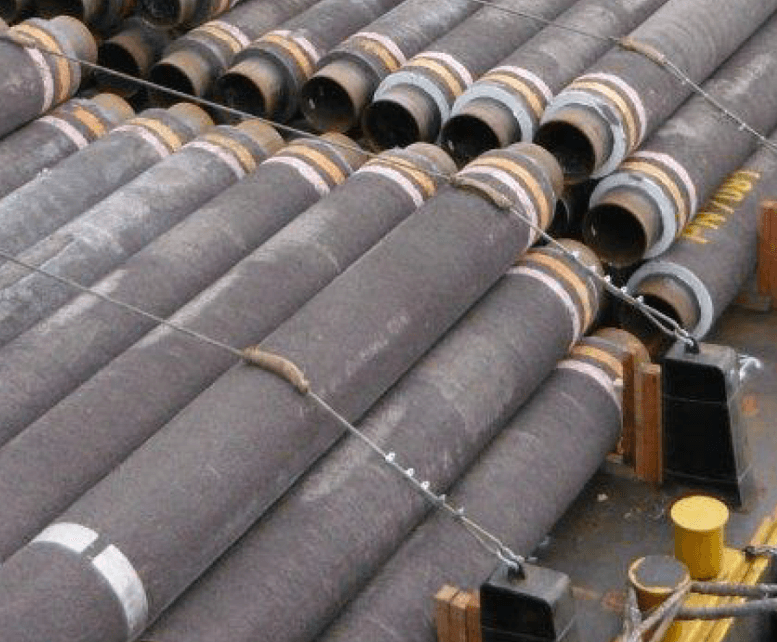
Pipe Transportation – An Introduction (Part 1)
(To read Part 2, click here) This is the first part in the 3-part series on Pipe Transportation. In this part we will discuss about pipes and their properties. In this article, we will talk about the transportation of pipes on ships. Pipes are needed for various...
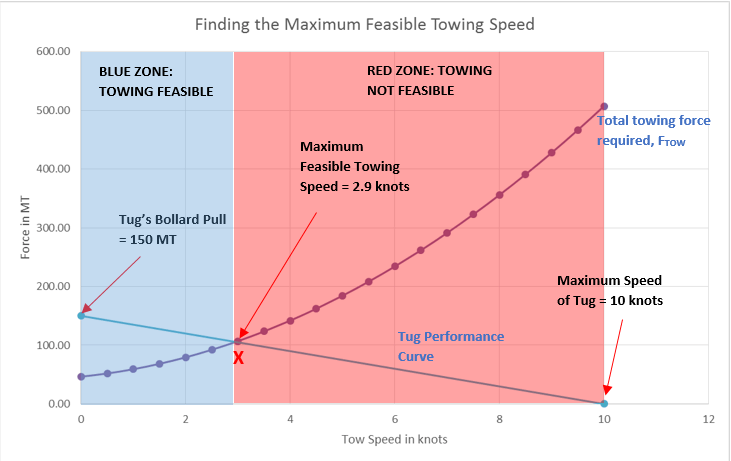
Bollard Pull Calculations – an Introduction (Part II)
Bollard Pull Calculations for Towing Operations Part II - Finding out the maximum feasible tow speed (To read Part I, please click here) Introduction This is Part - II of the two part article on Bollard Pull calculations. In the Part I we saw how to calculate the...
Please check out TheNavalArch’s product for planing vessel resistance estimation:
Interesting solution to a practical problem.