by Alessandro La Ferlita, Naval Architect
Ultimate hull girder strength represents the maximum capacity, of the hull girder beyond the structure fails.
In fact, if the vertical bending moment applied overcomes a certain maximum value, the ship can collapse (Figure 1) due to different phenomena as buckling and progressive collapse [1] of the compressed part.
Instances are famous cases of the oil tanker “Energy Concentration” that happened in 1980 and the container vessel “MOL COMFORT” in 2013.
Figure 1 Collapse of “Energy Concentration” [2]
The estimation of the ultimate strength plays an important role in structural safety and for reliability in terms of loads during the life of the vessel.
In general, the ultimate hull girder capacity considers the evaluation of the overall strength by summing up the general load capacities of individual elements such as plates, stiffeners, girders within the cross-section.
Methods for determining the ULS
Several rule models can be used for calculating the ultimate strength.
1) Smith method (Iterative approach)
2) ISUM (Idealized Structural Unit Method)
3) Non-linear FEA.
The first method is quite well known and prescribed by IACS.
The original idea comes from Smith at the end of 70’s which developed a simplified method to evaluate the ultimate strength basing his approach on the following assumptions [3]:
- the section of the ship to take into account is between two stiffened frameworks and consists of all the structural elements that contribute to longitudinal strength
- the collapse section remains plane when the curvature tends to increase or decrease;
- the behavior of the material constituting the resistant section is ideal elastic-plastic characterized by the load end shortening curve;
- the structural section is considered to consist of j elements (j → discrete number of elements) whose structural behavior is independent when the curvature is acting on the section.
The main steps (Figure 3) to consider for the procedure are the following [3] [4]:
- subdivision of the main cross-section in a defined type of element correspondingly into:
- Hard corner Element, which is generally constituted by two plates that do not lie in the same plane: one is horizontal and the other is vertical.
- Longitudinally stiffened plate element, with attached plating up to the midpoint between adjacent stiffeners on each side.
- Transversely stiffened plate elements, which are typical geometrical areas between stiffener elements and hard corner elements (Figure 2).
Figure 2 Subdivision – Hard Corner/Transversally stiffened Plate Elements/ Longitudinally stiffened plate element
Figure 3 Description of the Smith Method [3]
2. The stress-strain relationships of individual elements are carefully considered and obtained, taking into account: the influences of yielding, buckling, and the initial Neutral axis.
Regarding this second step, the stress properties of each element are defined using different curves that describe the relationship between the axial load and displacement. In general, it is possible to distinguish them according to their behavior (figure 4a) [5]:
(a) elastic without buckling;
(b) elastic-perfectly plastic without buckling;
(c) buckling/yielding without strength reduction beyond the ultimate strength;
(d) buckling/yielding with strength reduction beyond the ultimate strength.
This last behavior is quite realistic and its capacity decreases after its maximum value has been obtained.
In general, those curves could be determined by using empirical approaches or by nonlinear finite element method, using for example some software as ANSYS or ABAQUS. Nevertheless, direct methods are given by DNV GL which suggests using a specific formula for obtaining the corresponding stresses as shown in table 1.
Element Mode of failure Lengthened stiffened plate element or stiffener element Elasto-plastic collapse Shortened stiffener element
Beam column buckling
Torsional buckling
Web local buckling of flanged profiles
Web local buckling of flat bars
Shortened stiffened plate element Plate buckling
3. Forces are derived by multiplying the stress by the area of the element considered. The final sum of the forces above the neutral axis should be equal to the sum of the forces below the neutral axis; If this condition is not satisfied, it means that the initial position is shifted and a new one should be searched;
4. Verification that the new neutral axis (which guarantees the equilibrium of stresses) differs with a low tolerance value in respect to that one assumed at begin of the procedure. If this condition is not fulfilled, it is necessary to reiterate all the process basing the calculation on the last neutral Axis obtained;
5. In case the previous step is satisfied, it is possible to calculate the bending moment. After that, it would be necessary to increase the curvature of a certain delta of increment;
Residual ULS
The determination of the ULS plays an important role especially when the ship results damaged and the salvage operation is needed.
In fact, grounding or collision can lead to a reduction in the effectiveness of the structural elements and consequently to the reduction of ultimate strength.
Figure 4 Damage due to grounding [5]
In such circumstances, by neglecting the elements which belong to the cross-section (Figure 4) which do not carry anymore the longitudinal strength, it is possible to calculate the ULS (Figure 5).
In this context, the methods before mentioned could be applied, but paying attention to the symmetry/asymmetry of the damage
Figure 5 Residual ULS for different damaged scenario vs Intact ULSS [6]
RD Diagram
Paik et al. [5] proposed an innovative method for assessing the safety of a ship which has suffered damage grounding through the application of R-D (Residual Damage) Diagram.
Figure 6 Residual damage diagram [7]
They are obtained in the following way.
First of all, the characteristics of the ships, including geometry, dimensions, and material properties are defined. Then a limited number of probable damage scenarios representing all possible scenarios can be selected by a
probabilistic approach.
In practice, it means that a small number of probable scenarios for possible accidental or in-service damage are selected using for instance a sampling technique in which the random variables affecting the damage are probabilistically characterized.
Afterward, the GDI (grounding damage index) is defined for describing the damage severity for each of the considered scenarios.
The residual strength of the ships in the grounding damage scenarios is then calculated by using a simplified approach or by applying more complex methods, such as non-linear FEM (Finite Element Method).
Finally, the R–D diagram is established based on these calculations performed.
Furthermore, the GDI concept can be applied to determine the acceptance criteria for grounding strength performance [9].
For example, IMO (International Maritime Organization) specifies requirements that the ultimate longitudinal strength of all newly built ships be no smaller than 90% of the strength performance.
In general, those kinds of diagrams will be very useful for a first-cut assessment, immediately after it has been suffered a grounding, by knowing the damaged area.
Bibliography
[1] |
Ö. E. Bayraktarkatalb, “Effects of Key Factors on Hull Girder Ultimate Strength Estimation by Progressive Collapse Calculations,” Latin American Journal of Solids and Structures, pp. 2371-2392, 2016. |
[2] |
“www.shipspotting.com,” [Online]. Available: http://www.shipspotting.com/gallery/photo.php?lid=1688178. |
[3] |
DNVGL-CG-0128, “APPENDIX E HULL GIRDER ULTIMATE BENDING CAPACITY BY MULTI-STEP METHOD,” 2018, pp. 125-136. |
[4] |
Soares, A. W. Hussein & C. Guedes, Design Equation for the Ultimate Capacity of Double Hull Tankers Designed According to the Common Structural Rules, Lisboa, Portugal: Centre for Marine Technology and Engineering (CENTEC), Technical University of Lisbon, 2008. |
[5] |
M. F. Tetsuya Yao, “PROGRESSIVE COLLAPSE BEHAVIOR OF HULL GIRDER UNDER,” in Buckling and Ultimate Strength of Ship and Ship-like Floating Structures, Kidlington, Oxford, United Kingdom : Butterworth-Heinemann is an imprint of Elsevier Á, 2016, pp. 321 – 336 – 348 – 353. |
[6] |
DNVGL-CG-0128, “APPENDIX E HULL GIRDER ULTIMATE BENDING CAPACITY BY MULTI-STEP METHOD,” DNVGL-CG-0128, 2018, pp. 125-136. |
[7] |
J. K. Paik,D. K. Kim,P. T.Pedersen,H. Kim , “DEVELOPMENT OF A RELATIONSHIP BETWEEN RESIDUAL ULTIMATE LONGITUDINAL STRENGTH VERSUS GROUNDING DAMAGE INDEX DIAGRAM FOR CONTAINER SHIPS,” Proceedings of the ASME 31st International Conference on Ocean, Offshore and Arctic Engineering OMAE, vol. 2, pp. 1-10, 2012. |
[8] |
Ji-Myung Nam and Joonmo Choung , “Residual Longitudinal Strength of a VLCC Considering Probabilistic Damage Extents,” Proceedings of the Twenty-second (2012) International Offshore and Polar Engineering Conference , 2012. |
[9] |
Do Kyun Kim, Preben Terndrup Pedersen, Jeom Kee, “Safety guidelines of ultimate hull girder strength for grounded container ships,” Safety Science, vol. 59, pp. 46-54, 2013. |
Please do checkout TheNavalArch’s simple-to-use and effective calculator for Hull Ultimate Strength – called the Hull Grounding Damage Index (GDI) calculator
Disclaimer:
The views, information, or opinions expressed are solely those of the author and do not necessarily represent those of TheNavalArch Pte Ltd and its employees
Alessandro La Ferlita
Naval Architect & Marine Engineer
Naval Architect and Marine Engineer

The why and how of freeboard calculation of a ship
Introduction Freeboard is a common term used in vessel operations. Freeboard is the smallest vertical distance between the waterline and the freeboard deck (generally the upper deck) along the length of the vessel. The term ‘smallest’ is of significance, as the height...
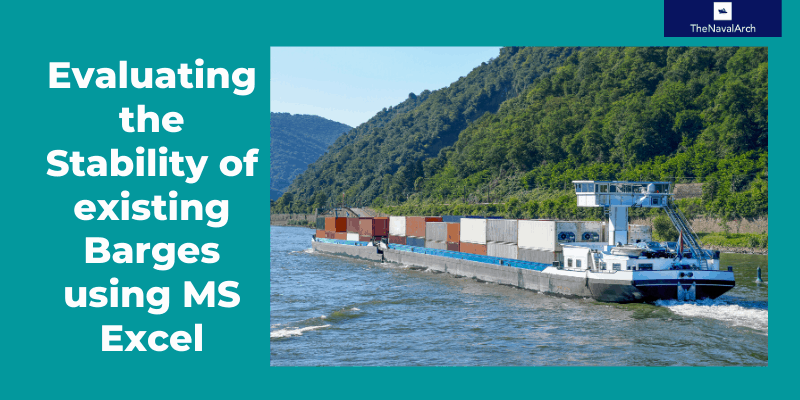
Using MS Excel to evaluate the Stability of existing Barges
Barges are the simplest, and yet most widely used of marine vehicles. They are used for a variety of purposes ranging from carrying cargo in bulk or liquid, to even carrying passengers for short inland cruises. Barges are mostly towed by another barge called a tug,...
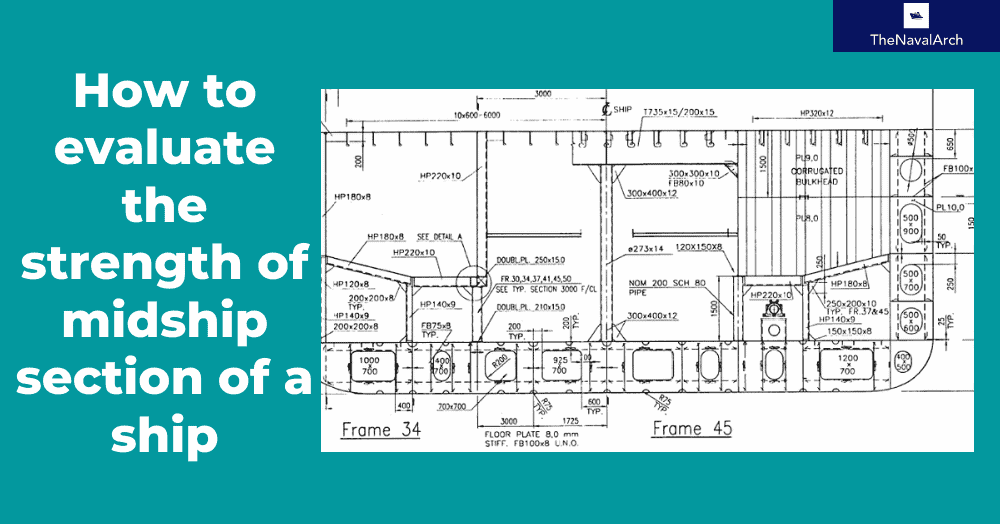
How to calculate the strength of Midship Section of a Ship
The mid-ship section of a ship is a defining structural drawing of the vessel. It represents the most critical structural parameter of the vessel – its global strength. To assess how much of the bending moment (hog and sag) the vessel can tolerate, it is important to...
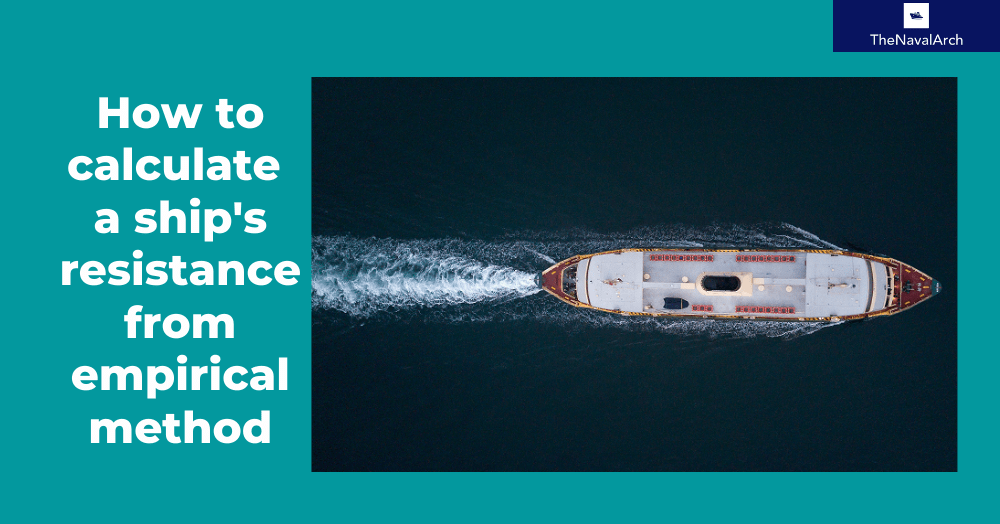
How to use empirical formulas to estimate the resistance of a Ship
How to use empirical formulas to estimate the resistance of a Ship Resistance estimation holds immense importance in the design stage of a vessel. Based on the results of the resistance estimation of a vessel, the selection of the right propulsion system is done....
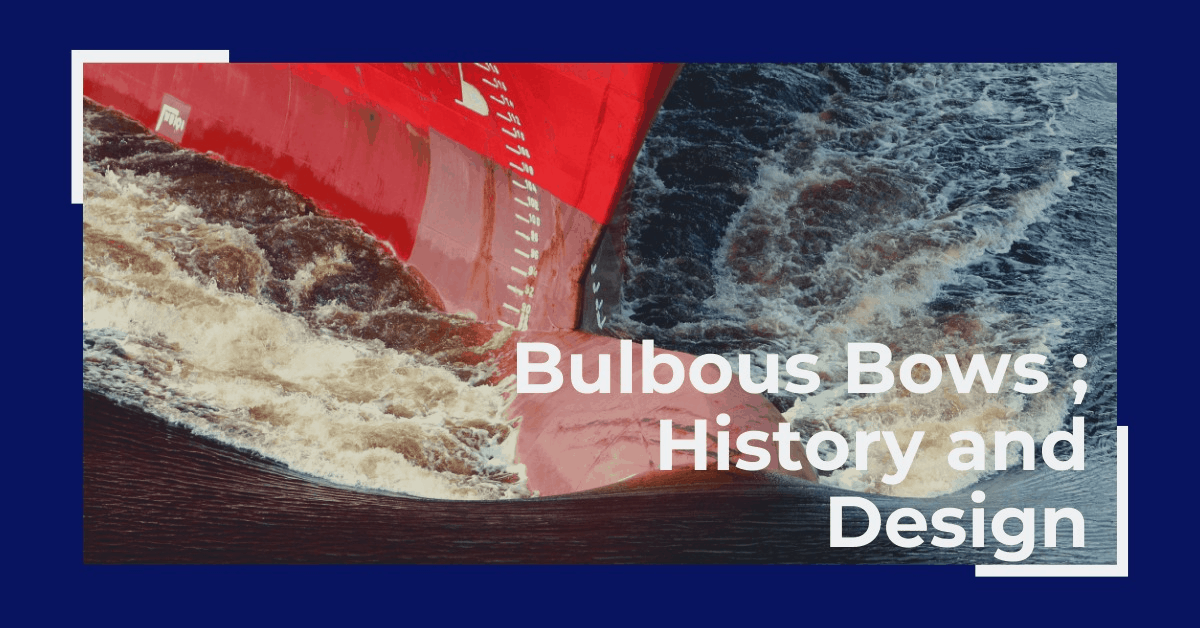
Bulbous Bows – History and Design
by Bijit Sarkar, Naval Architect Introduction The eternal search of a naval architect – a perfect bow. Sadly, it never exists. Different bow forms are good for different types, sizes of vessels and seaways. What does a naval architect want out of the bow he designs?...
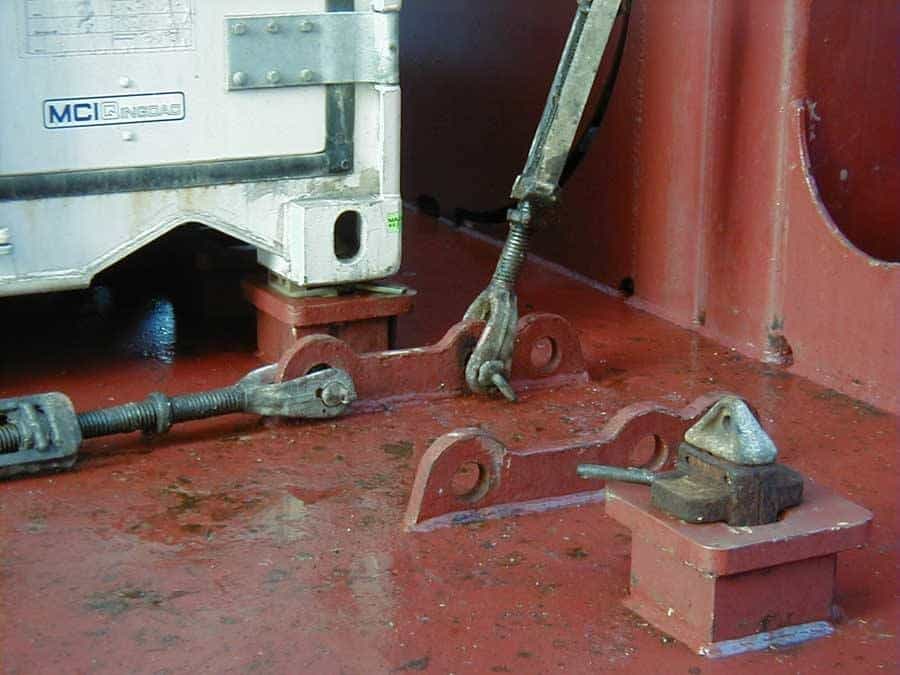
Designing a pad-eye: little items with big intricacies
Pad-eyes are one of the smallest and most universally used structural items in the maritime and Oil & Gas industry. They are used for a variety of purposes too: from a simple seafastening of a cargo to deck of a vessel, to complicated lifting operations involving...
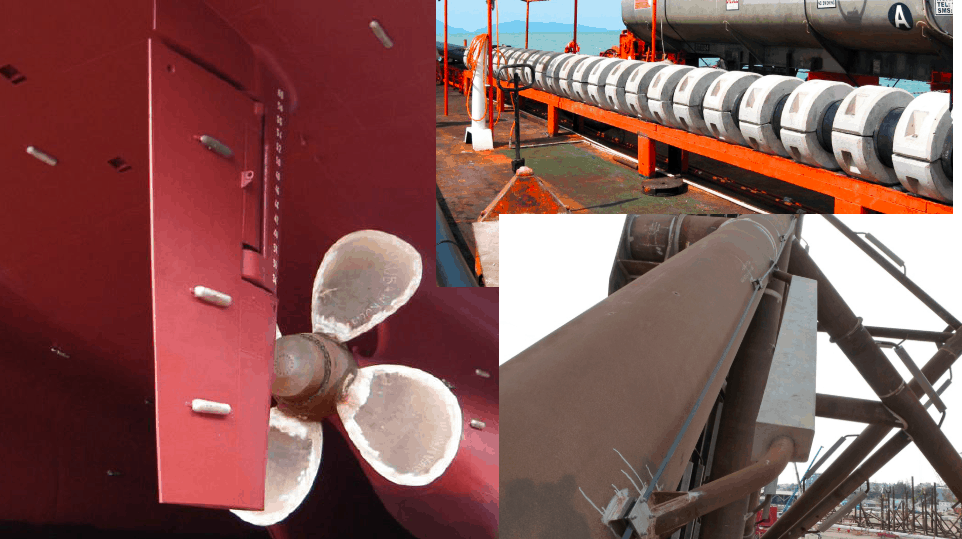
Cathodic Protection – Ships, Offshore Platforms, FPSO’s and Pipelines: a comparison
Cathodic protection of a structure is an exercise which requires close study of the structure on which it is going to be implemented. The type and quantity of cathodic protection by anodes will depend upon multiple factors: the Geometry of the Structure, the...
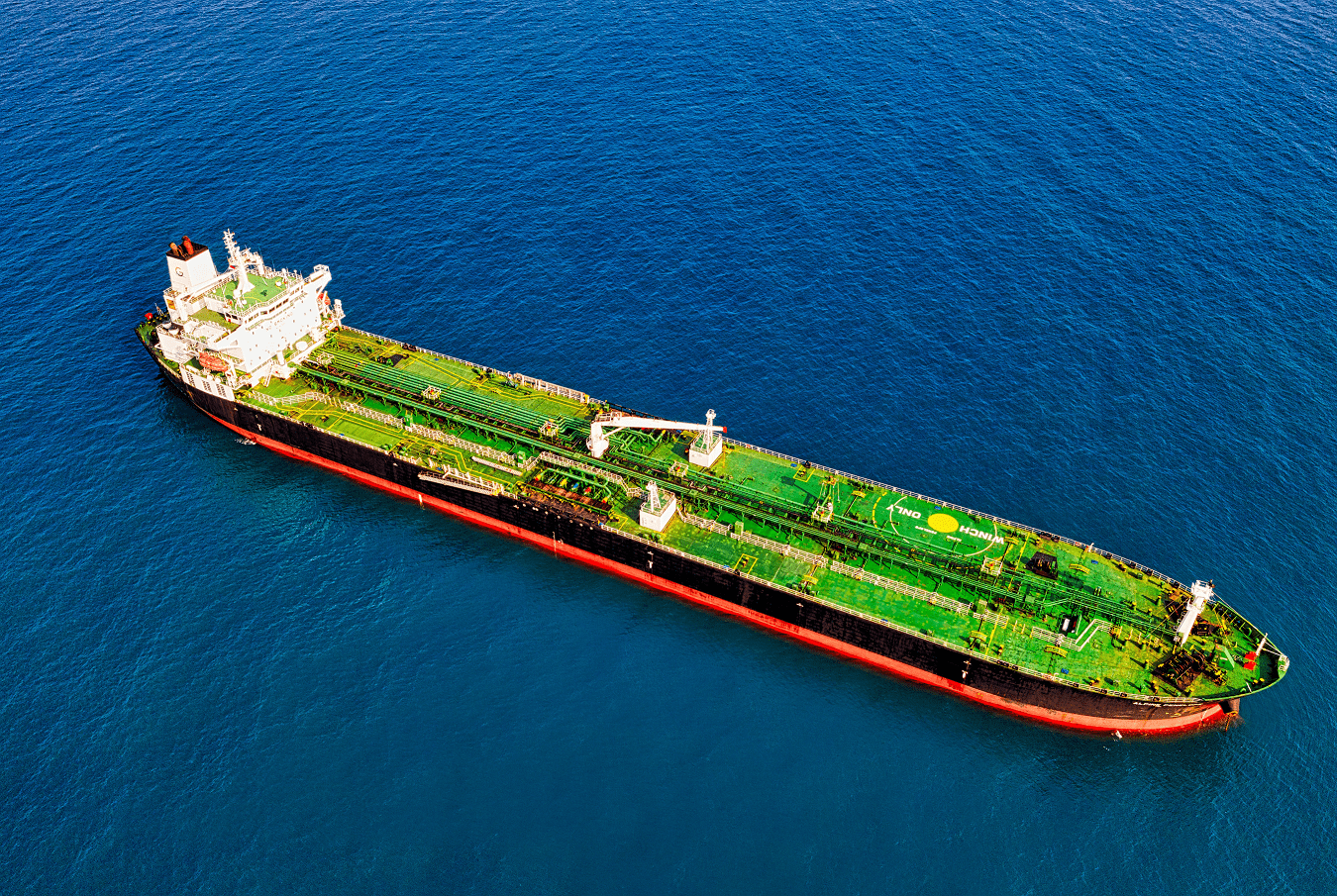
Role of a naval architect – a walkthrough (Part – 1)
This is the first in a series of articles on 'Role of a Naval Architect' by Mr Bijit Sarkar, a Naval Architect with 35+ years of experience in ship design and shipbuilding. I would define a naval architect as one who has the ability to greet the client as he/she walks...
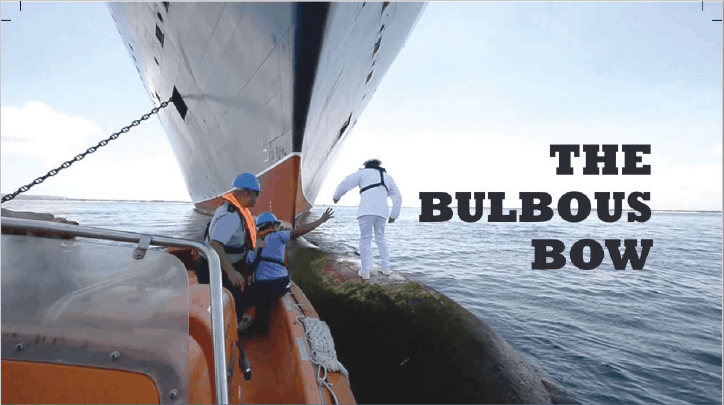
The bulbous bow – why some ships have it and others don’t
By Tamal Mukherjee, This is the Part 1 of a two part article on the Bulbous Bow. Part 2 can be accessed here *This article originally appeared in May 2019 edition of Marine Engineers Review (India), the Journal of Institute of Marine Engineers India. It is being...
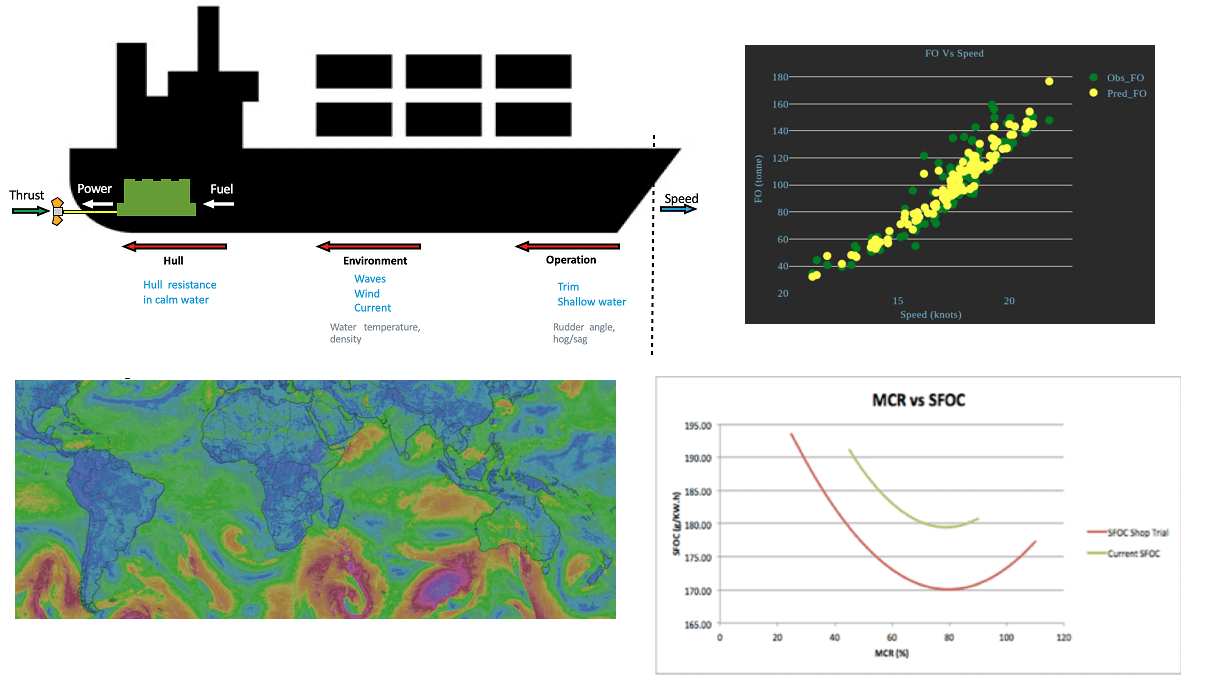
Removing Human Error in Ship Performance Analysis
Introduction Shipping is the most dominant means of transport that facilitate global trade. Over 90% of world trade is done by ships[1]. Fuel onboard ships, commonly referred to as "bunkers", has become the largest cost item of a ship's Operational Expenses (OPEX),...