Introduction
In an earlier article, we saw how to design stoppers for seafastening. Stoppers are items that are used to contain the translation movements (longitudinal and transverse directions) of a cargo on the deck/hold of a vessel.
That brings us to the question – what about tipping of the cargo? If the cargo is subjected to external forces that cause it to tip, how do we protect the cargo against tipping?
Thinking in basic terms, to prevent cargo from tipping/overturning, we will need something that pins or clips it to the deck. Such a seafastening item is called a ‘Clip’ or a ‘Dog Plate’. Imagining such an item, it can be an ‘L-shaped’ structure that clings on to the base of the cargo. If we see the figure below, the dog plate is like a jaw that clamps down on the base frame of the cargo. We can also see that this kind of structure will help prevent the overturning of the cargo, as compared to stoppers which can prevent only translation. At times, both dog plates and stoppers may be used together on the same cargo with dog plates resisting overturning and stoppers resisting translation.
Designing a Dog Plate:
In this section, we’ll see how do we go about designing a dog plate for a particular operation.
Any design takes up the following flow:
- Evaluate the forces acting on the structure
- Check the stresses on the structure due to the forces
- Iterate the design until the stresses are within the acceptable levels
Forces on the structure:
The cargo on the vessel will experience forces in the three directions – longitudinal, transverse, and vertical (uplift), besides the self-weight of the cargo. The first three forces depend on the environment in which the vessel is operating, and one simple but conservative way of calculating these forces is to follow DNVGL guidelines (See DNVGL-ST-N001, also see our product on Cargo Forces and Accelerations)
Longitudinal or Transverse Forces
In the figure below that shows the plan of a vessel’s deck carrying cargo, we can see that there are multiple dog plates in each direction to resist the respective force (transverse or longitudinal).
If the number of dog plates in the transverse direction is nT and the total transverse force on the cargo is FT, then the transverse force on a single dog plate in the transverse direction is
FT1 = FT/nT
Similarly, in the longitudinal direction, the total longitudinal force divided by the total number of dog plates in that direction gives the force on one dog plate.
Uplift Force
The uplift force is a vertically upward force due to the cargo motion. It is calculated from a motion analysis or from empirical relations (See our product for Cargo Forces and Accelerations).
Self-Weight of Cargo
The cargo also experiences its own self-weight that acts vertically downwards.
The force diagram of the Cargo can be drawn as below:
We can see that given the location of the dog plate, the following forces and moments will be experienced by it:
- The transverse force FT will be borne by all the dog plates.
- An overturning moment on the whole cargo, MT, due to FT, Uplift Force, and Self-Weight will also be borne by all dog plates. We can see that while FT and FV will cause the cargo to tip, the restoring moment due to self-weight protects it from tipping.
MT = FT x H/2 – W x B/2 + FV x B/2
The above force and moment can be divided by the number of dog plates (nT in the transverse direction) to give the force and moment per dog plate.
FT1 = FT/nT
MT1 = MT/nT
Translation of forces to the Dog Plate
The net overturning moment MT1 on a single dog plate translates effectively to an uplift force on the dog plate due to the moment. Considering the uplift force to be acting at the dog plates on either side, the effective uplift force on each dog plate is
FV1 = MT1/B
where B is the width of the cargo.
Next, we see the force diagram of the Dog Plate itself:
We can see that the following forces are acting on the dog plate:
- The translation force FT1, which gets directly translated from the cargo
- The uplift force FV1, which occurs due to the overturning moment
Stresses on the dog plate
The above two forces lead to various stresses for which the dog plate needs to be analyzed:
- Shear Stress: The force FT1 leads to shear stress on the dog plate
- Tensile stress: The effective tensile force is calculated from the moment of the two forces FT1 and FV1 about the base, divided by the length of the base, L2.
- Bending Stress: bending moment at the base is calculated by adding the bending moments due to FT1 and FV1 at the base.
- Weld Check: The weld of the dog plate to the deck also needs to be checked similarly for shear, tensile and bending stresses
By calculating the forces and moments applicable, the stresses can be calculated, and the suitability of the dog plate evaluated. Some sample calculations are shown below:
Disclaimer: This post is not meant to be authoritative writing on the topic presented. thenavalarch bears no responsibility for the accuracy of this article, or for any incidents/losses arising due to the use of the information in this article in any operation. It is recommended to seek professional advice before executing any activity which draws on information mentioned in this post. All the figures, drawings, and pictures are property of thenavalarch except where indicated, and may not be copied or distributed without permission.

TRANSPORT VESSELS FOR FLOATING WIND
By Alan Crowle, BSc, MSc, CEng, CMarEng, FRINA, FMAREST, FSCMS Masters by Researcher, University of Exeter, College of Engineering, Mathematics and Physical Sciences, Renewable Energy Group SUMMARY Floating wind turbine construction is a large logistical exercise. The...
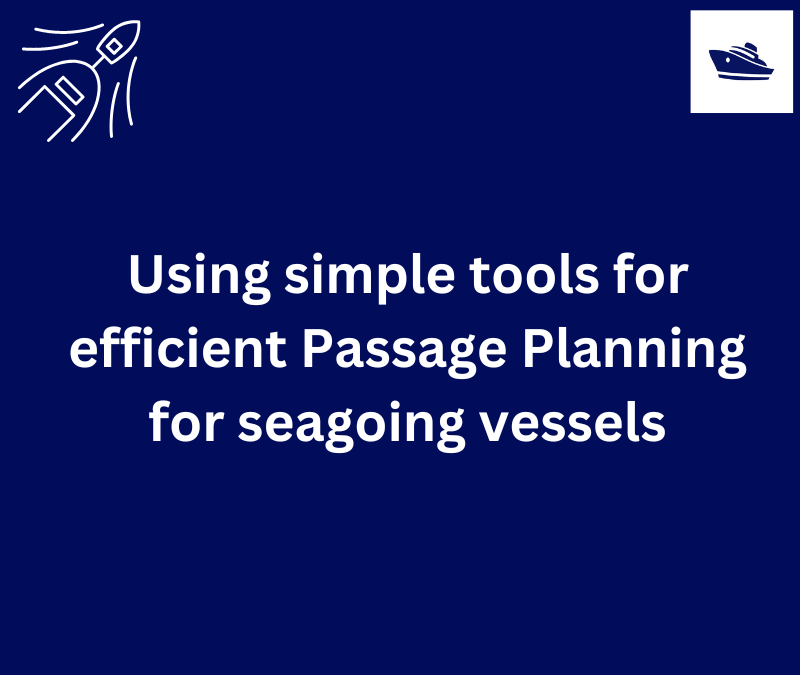
Using simple tools for efficient Passage Planning for seagoing vessels
Introduction Planning a vessel’s voyage is a critical detailed exercise, and the main goal is to ensure safe and efficient passage between two ports. The Master has the responsibility for the vessel voyage planning, but very often he delegates the actual voyage...
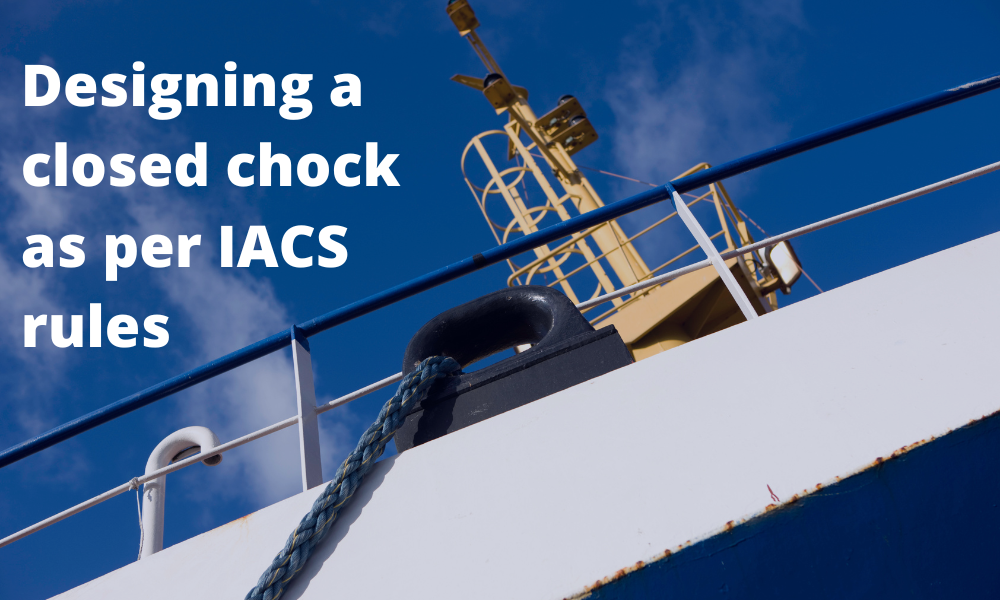
Designing a closed chock as per IACS rules
Introduction Chocks are used universally for mooring and towing operations on ships. For towing operations, Chocks are used for guiding the towing rope from the winch through the outer shell of the vessel to the tug. For mooring operations, the chock is used to...
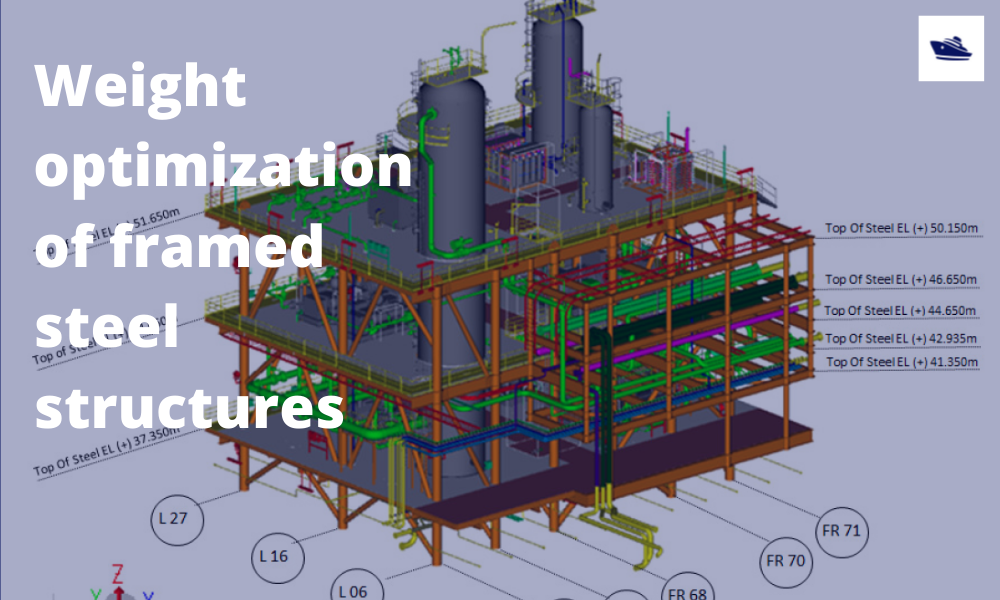
The Optim22 Method of Weight Optimization of Framed Steel Structures
1 Abstract A semi-automated structural weight optimization system is presented for framed structures of post and beam construction which is based on basic structural member design principles. The approach is to adjust member properties in a manner that...
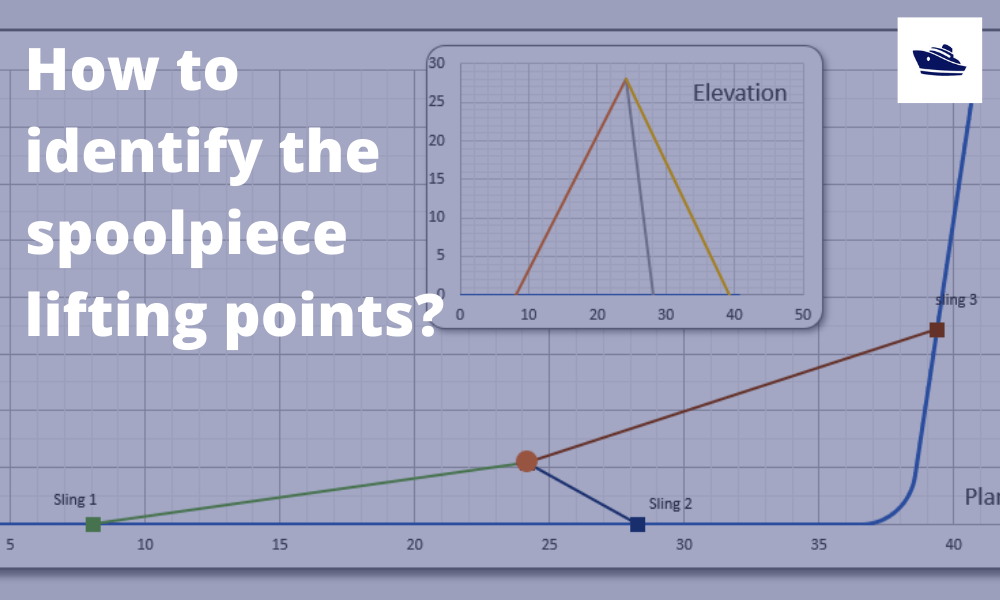
How to identify the spoolpiece lifting points?
In the offshore construction industry, the connection between the newly installed pipeline and the riser is accomplished via a series of ‘spoolpieces’ (or spools). The spool is fabricated by welding pipe joints to form an L-shaped, Z-shaped, or possibly a straight...
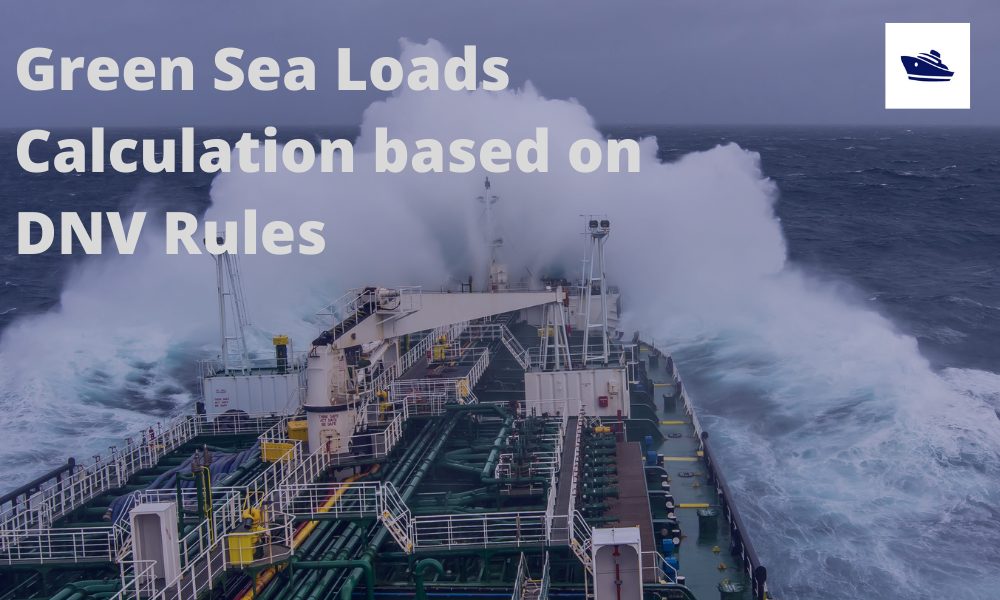
Sea Pressure Loads Calculation based on DNV Rules
Introduction Sea pressure loads are an important factor in the structural design of a vessel. What is sea pressure load? As the term suggests, it is the external pressure on the vessel due to the surrounding sea. What kind of pressure it is, and how to...
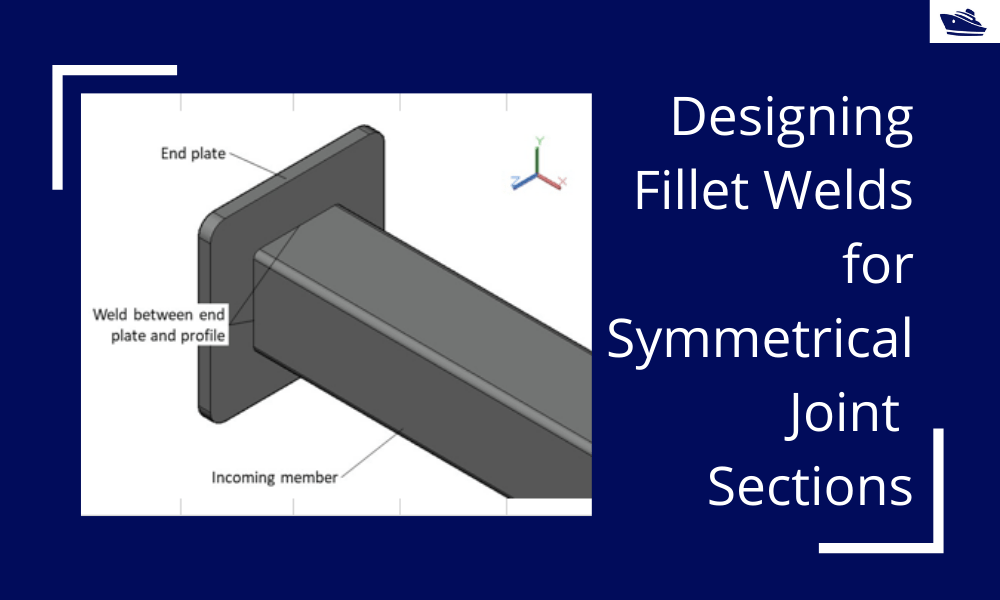
Designing Fillet Welds for Symmetrical Joint Sections
Introduction Fillet welds are the most commonly used weld types in marine structures. A fillet weld is used when there are two pieces of metal that are joined perpendicular to each other or at an angle. In this article, we will explore how to select the right size...
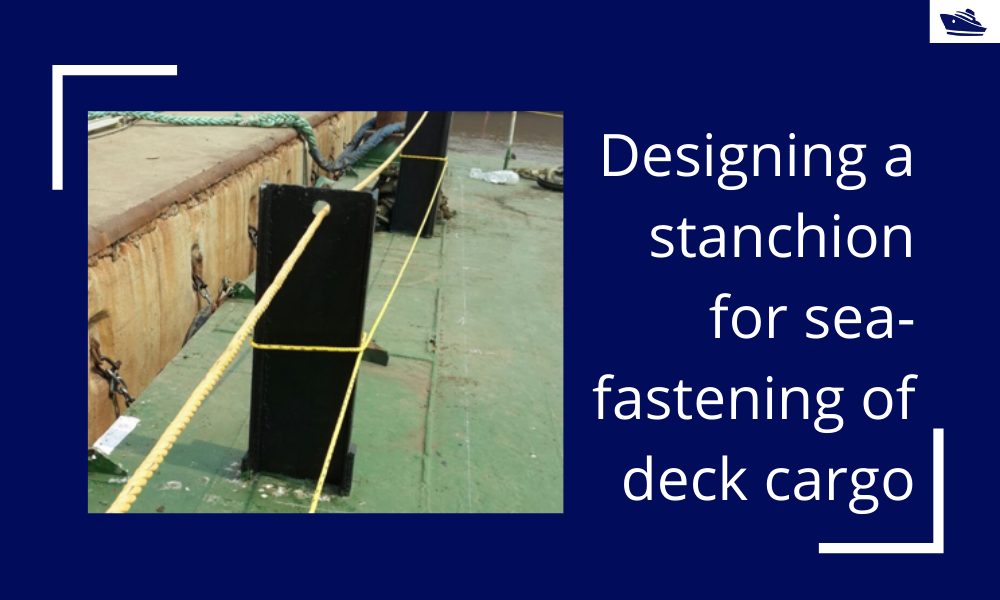
Designing a stanchion/stopper for sea-fastening of deck cargo
Introduction Stanchions – a familiar term for mariners and ship designers. What are Stanchions? A stanchion is generally a vertical pipe or beam which is used to support some structural item or provide support rails on the deck. In ships, the most common type of...
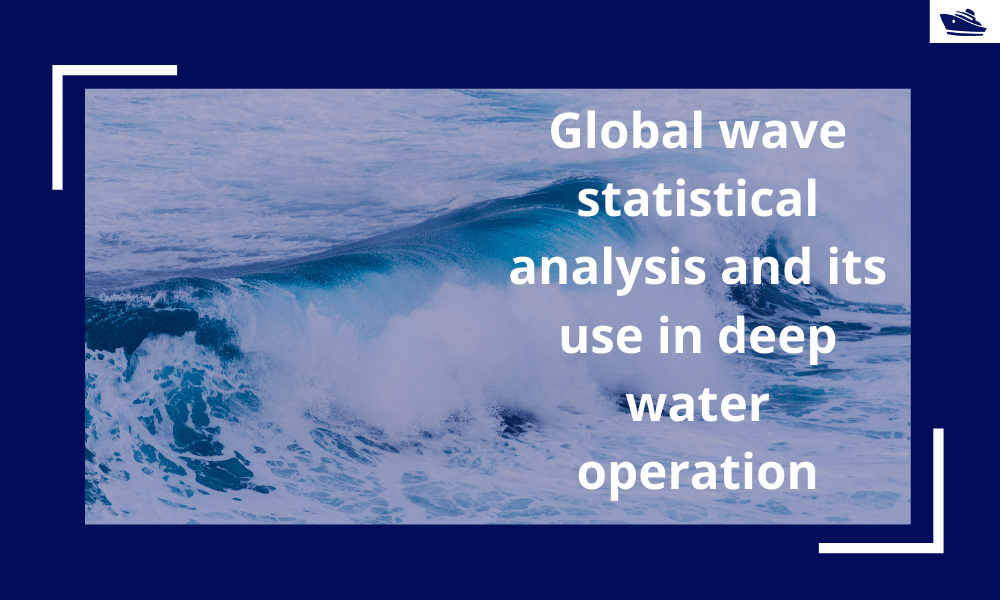
Global wave statistical analysis and its use in deepwater operations
Why do we need wave analysis? For the design of offshore operations such as installation and transport of offshore structures, as well as lifecycle design of floating and fixed structures, knowledge of extreme waves as well as the probability of different sea-states...
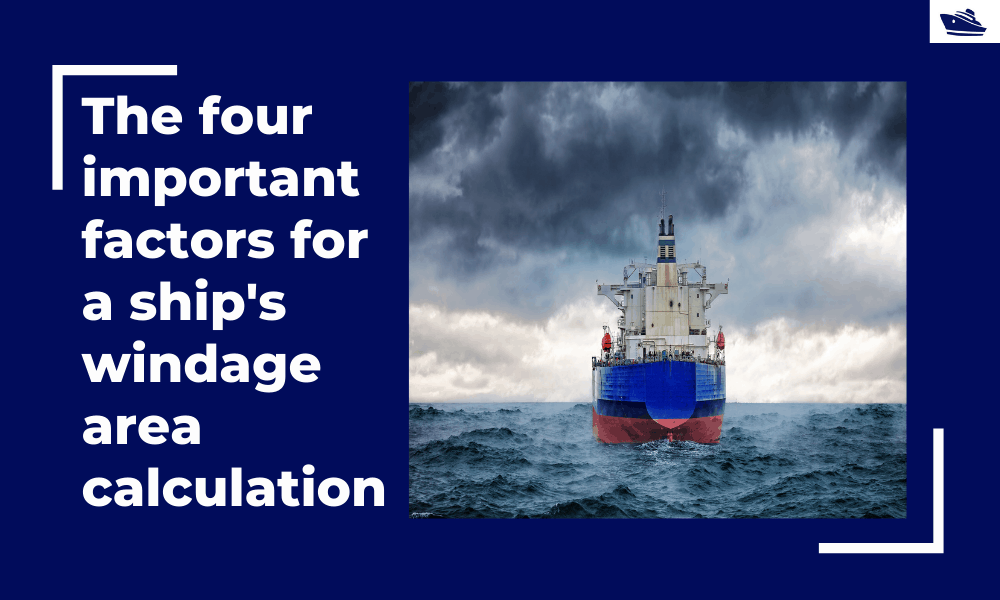
The four important factors for a ship’s windage area calculations
Introduction The windage area of a vessel or offshore structure is the area that is exposed directly to the wind. As is obvious, this is the area of all items above the waterline. This will include Part of the hull/offshore structure above the waterline...
Thanks alot for this brief knowledge
NEED FOR PRINCIPLES OF DESIGNING SEAFASTENINGS